汽车模具行业:需要高速、高精、高可靠性设备
——汽车模具市场将迎来自己的春天
目前,我国每年的汽车产销量都以极快的速度增长,我国汽车工业的发展,极大地推动了我国汽车模具行业的发展。如今,我国已进入汽车制造大国,而汽车零部件的需求规模比整车还大,这些零部件90%以上都靠模具生产,这些强大的市场需求大大推动了汽车模具工业的发展。
在汽车工业飞速发展的同时,国外汽车制造企业一致看好中国市场,纷纷进入中国采购汽车零部件。随着国际上汽车制造企业开始实行零部件全球化采购策略及国际跨国汽车企业推行本土化策略,我们的汽车模具也迎来了发展的黄金时期。
汽车模具国产化基本实现
据天津汽车模具有限公司副总经理、总工程师常世平介绍,20世纪80年代之后,我国开始从国外引进汽车模具的生产设备和加工技术,但是,这个时期,中国汽车的更新换代发展缓慢,汽车车型主要靠国外引进,且大部分同时引进模具。国内的汽车模具生产能力落后,也基本上是自产自用,顶多在汽车厂家之间搞些行业Ð作,几乎没有独立的专业汽车模具厂。20世纪90年代后期,随着国家对汽车行业的重视,众多汽车及模具厂商开始重视汽车模具的研发和制造,开始在汽车模具上加大了投资,汽车模具企业大量涌现,才逐渐成为一个独立的行业,汽车模具才开始逐渐形成商品进入市场。随着汽车模具的商品化,客户要求更高,如何满足客户需求就成为了模具厂商的追求。常世平告诉记者:“汽车模具行业的首要目标就是替代进口,实现汽车模具国产化。”但由于中国合资汽车公司比较多,因此当时很多汽车模具还是靠国外进口,国内汽车模具只能起到辅助和配角的作用。
近年来,中国汽车模具有了长足发展,在世界范围来说,已经后来居上,已经成为模具大国。但中国的汽车模具出口量还很少,这说明我们的汽车模具还远不如塑料模具出口发展的那么快。“中国汽车模具出口少的主要原因,还是因为汽车模具技术门槛比较高。”在常世平看来,在之前的汽车模具发展历程中,国外客户的准入门槛高,国内汽车模具项目管理、设计制造技术力量薄弱、缺乏实际生产经验、国际营销能力差等各方面都制约着我国汽车模具更快发展。但总的来说,中国的汽车模具的发展速度还是非常快的。“国内已基本上可以生产所有的汽车模具,缺的不是设备和技术,而是成熟的有验的高端人才。可以这样说,目前我们和德国、日本等发达国家的汽车模具相比差别并不大,主要差的也不是技术,而是管理和经验。”正如常世平所说,现在除了特别高端的汽车模具没有实际设计制造验外,中国基本上都能实现汽车模具国产化,而且也在开始扩大模具出口份额。
大型化、复杂化成为汽车模具发展趋势
汽车模具特别是覆盖件模具都属于大中型模具,大型化是汽车模具的一大特点,单套模重量就可达四五十吨,就是中小模具也是以吨为重量单位的。“像车门外板等以前都是一个标准的模具,现在由于普遍采用整体侧围技术,结果冲压线吨位和台面越来越大,其他小一些的制件可能也会两个甚至多个零件组合在一套模具内,这样造成了汽车关键模具的大型化和复杂化。”常世平介绍说。
“除了大型化,汽车模具还有一个加工特点,就是以自由曲面加工为主,这就要求加工机床的动态精度非常高,同时为了减少加工的残留量和保证加工效率,小间距的高速、高精度加工成了最常用技术。”据常世平介绍,当汽车模具大型化以后,会带来很多新问题,几何尺寸大,加工精度靠机床精度已很难保证,例如:原来没有注意到的昼夜温差的变化,现在也会严重影响模具加工精度。在北方经常昼夜温差超过10℃,这种温差带来模具收缩膨胀量就足以使上下模匹配超差。所以,对于大型模具加工车间一般都需要采用恒温。
大型汽车模具的另一个特点就是复杂的型腔比较多,因此对加工深度、垂直度、平面度等要求都很高,对于机床和道具的高刚度、高精度、高动态静态等要求也就很高。这些特点综合在一起,也就造成汽车模具的加工难度非常大。常世平告诉记者:“汽车模具在设计阶段就要考虑所有的精度问题,加工过程就是保证各种要求实现的过程。不能加工完之后,还要过大量的修改和后续加工来完善,这样不仅质量无法保证,加工周期也会严重拉长。”
除了高速加工之外,模具加工的另一个特点就是超硬加工。因为模具表面的硬度要求都很高,如果精加工后再做淬火处理的话,会造成模具的热变形,模具精度无法保证。为了实现零件既要硬度高还要精度高,现在往往实行淬火后再加工。常世平认为,汽车模具加工的过程中既要实现大尺寸、高速度,又要实现高精度,还要实现超硬加工(硬度能够达到HRC60以上),这样就造成了汽车模具加工的难度非常大。
对于复杂型腔和多功能复合模具,随着制件形状的复杂化,也必须要提高模具的设计制造水平,多种沟槽、多种材质在一套模具中成形或组装成组件的多功能复合模具,都需要靠在加工编程阶段对加工程序的深化来实现,改善加工工艺对高深孔腔的综合切削能力以及提高加工稳定性。
“国内汽车用户对于汽车模具的要求,首先就是低成本,因为在汽车制造开发成本中,模具占绝对大头。现在汽车的品种和新车开发越来越多,降低开发成本往往是新车能否成功的关键”。常世平介绍说,“由于中国汽车单一品种车的产量在逐步上升,因此对于汽车模具的长寿命,也提出了越来越高的要求。”
随着汽车产量提高,冲压设备性能的提升,为追求冲压效率,冲压的速度也越来越快,这就要求模具在热变形、高精度、高稳定性等方面的性能更好。汽车模具的精度越高,稳定性越好,使用寿命也就越长。随着汽车模具的制造水平的提高和越来越成熟,中国的汽车模具已能够很好地解决客户的这些硬性需求,并已达到了世界水平。
汽车模具加工大量需求高速高精加工中心
随着汽车模具向更高水平发展,对加工设备提出更高的要求。成型零件的日渐大型化,提高冲压生产率要求一模多腔,大吨位的汽车模具重达50~70t,这就要求模具加工设备要有比以往更大的工作台,大的Y轴和Z轴行程,还要有大承重、高刚性,高一致性。随着模具钢材料硬度提高,又要求模具加工设备具有热稳定性、高可靠性。模具加工的精细化使加工设备的复合性、高效性更加引人关注。高速铣削具有的可加工高硬材料、加工平稳、切削力小、工件升温变形小等诸多优点使模具企业对高速加工日益重视。
“对于汽车模具来说,最主要的加工设备就是龙门加工中心,其中一部分是五轴或者是五面加工,相对来说五面加工中应用的最为广泛,但不管采用什么设备,都要满足汽车模具高速、超硬、高精度、高刚度等加工特点。”常世平介绍说。由于汽车模具加工基本上都是24小时连续加工,因此对加工设备的可靠性也提出了很高的要求。程序化、无人化也是汽车模具加工的一个特点,这就要求加工设备具有更多的功能,更好的自动化配置。像自动换刀、自动找正等功能的配备,才能减少加工人员的需求。
“为了保证加工精度和一致性,模具加工时希望能够一次装夹完成全部加工,但实际加工过程中发现,要实现这样的要求也是很困难。这样对机床的要求也就更高,粗加工时要求高进给量,精加工时要求高速,淬火后又要求超硬加工,同时还要五轴加工,如果这些功能都在一台机床上体现,就会造成机床的成本太高,而且,在同一时间内可能只用到简单的几个功能,其他功能闲置,花几台机床的成本,却同时只能利用一台机床的功能,造成很大的浪费。”据常世平介绍,现在最常用的方法就是分工序加工,比如分粗加工和精加工,或者是分粗加工、半精加工和精加工。“总的来说,功能越多,机床的成本就会越高,而效率却体现的不是很明显。只是为了减少装夹次数,减少加工准备时间,在设备上多花的钱与提高的效率相比不成比例,这样并不合算的。”
在这次金融危机爆发中,中国的汽车行业没有受多大影响,反而是逆势而上,2009年中国的汽车产销都夺得了世界的头把交椅。但对于汽车模具行业来说,2009年确是很惨的一年,经历了从创建行业以来最大幅度的下降。国内外各大汽车厂商为了应对金融危机,纷纷削减了新车研发的投入,汽车模具订单严重缩水。随着世界经济的回暖,2009年大量模具需求的空缺,将在2010年及今后的几年得到有效的填补,汽车模具市场也将迎来自己的春天。
声明:本网站所收集的部分公开资料来源于互联网,转载的目的在于传递更多信息及用于网络分享,并不代表本站赞同其观点和对其真实性负责,也不构成任何其他建议。本站部分作品是由网友自主投稿和发布、编辑整理上传,对此类作品本站仅提供交流平台,不为其版权负责。如果您发现网站上所用视频、图片、文字如涉及作品版权问题,请第一时间告知,我们将根据您提供的证明材料确认版权并按国家标准支付稿酬或立即删除内容,以保证您的权益!联系电话:010-58612588 或 Email:editor@mmsonline.com.cn。
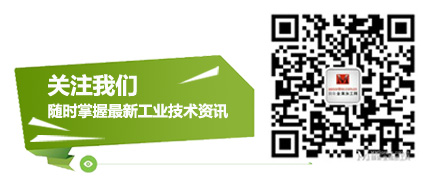
- 暂无反馈