模具加工中的关键——高速加工
近年来,高速加工(High Speed Cuting)技术的发展迅速,为提高模具制造水平、产品质量提供了新的发展方向。
阐述了在模具加工中实现高速加工所必需的一些关键技术,及高速加工技术在模具制造中的意义,并通过与常规的加工方式EDM的对比,描述了高速加工的优越性和局限性。同时以加工实例说明高速切削是现代模具加工的发展方向之一。
1 高速加工参数
在利用高速加工技术过程中,典型的高速切削加工参数有切削速度(指刀具切削处的切削线速度)、进给速度、主轴转速、刀具直径、切削深度、切削量等。一般而言,切削速度依据被加工模具材料和使用的刀具材料不同而变化,由经验准则可查出不同材料的刀具在切削钢材时的切削速度的范围。根据主轴转速与刀具的直径和切削速度关系式N=V×1000/(p×D)(r/min)计算出需要的主轴转速:进给量与刀具的主轴转速有关,它们的关系表达式为F(进给量)=单刃进给量×刀具刃数×主轴转速(mm/min)。通常,单刃进给量为0.1~0.25mm:每分钟的切削量=F×A d×Rd(mm3/min)。
2 高速切削加工与常规加工的比较
高速切削加工与常规的数控加工方法主要区别在于进给速度、加工速度和切削深度这三个工艺参数值不同。高速切削加工采用高进给速度和小切削深度(图2),而数控加工则采用低进给速度和大切削深度。另外,高速切削加工对机床主轴、切削刀具、计算机数控系统、伺服进给系统和数控编程方法的要求与常规的加工方式不同。过去模具的型腔加工是电火花(EDM)一统天下。但近年来,除了窄缝,深槽以及很细的纹理,非用电火花加工的以外,一般形状不太复杂的型腔及三维轮廓已能在高刚度的铣床和加工中心上用涂层铣刀进行高速加工,其加工效率比EDM高。而实际上,高速铣削更适合于加工形状不是很复杂的浅型腔模具,而对于深型腔和具有内清角的型腔模具,表面有花纹或图案的模具加工起来也存在一定的困难。事实上高速铣削和电火花在型腔模具的制造中是相辅相成的,在型腔模制造过程中,采用什么样的加工方式主要取决于型腔的几何形状、材料的硬度和所要求的工艺参数。
高速切削加工及其精密性生产实践表明,与传统切削加工相比,用高速加工容易生产和剪断切屑,当切屑厚度减小时,切屑温度上升,切屑更为碎小。而当应力和切屑都减小时,刀具负载变小,同时,由于产生的摩擦热减少,大量的切削热量被高速离去的切屑带走,故模具和刀具的热变形很小,模具表面没有变质及微裂纹,因而大大改善工件的加工质量,并且有效地提高其加工精度。同常规的加工相比,高速切削加工具有加工循环时间短、所需的刀具数少、切削应力小、产生切屑量大、加工精度高等特点。一般来说高速加工精度可达10?m以下,表面粗糙度Ra1?m以下。能有效地减少电加工和抛光工作量。
刀具寿命在高性能计算机数控系统的控制下,高速加工工艺能保证刀具在不同速度下工作的负载恒定。再加上刀具每刃的切削量极小,有利于延长刀具使用寿命。
淬硬模具的加工高速加工可以在高速度、大进给的方式下完成淬硬钢的精加工,且可达到很高的模具表面质量(Ra0.4?m),效率比常规方式高出4~6倍,所加工的材料硬度高达62HRC。而且由于高速加工切削量少,提高了加工及其后续表面光滑度,所以省去了过去机加工和电加工的磨削和抛光工序。
3 高速加工的刀具
高速切削刀具必须与加工的模具材料有较小的化学亲和力,具有优良的机械性能和热稳定性,即良好的抗冲击、耐磨损和抗热疲劳的特性。目前,陶瓷、立方氮化硼(CBN)、涂层硬质合金等刀具均可作为高速切削模具钢件的刀具材料。如用聚晶方法得到的聚晶立方氮化硼(PCBN)的刀片硬度达3500~4500HV,已成为高速切削淬硬钢的首选刀具材料。刀具的涂层技术是提高高速切削能力的关键技术之一。
4 高速切削加工对机床的要求
主轴要求动平衡性能好,刚性好,回转精度高,有良好的热稳定性能,能传递足够的力矩和功率,能承受高的离心力,带有测温装置和冷却装置。如Makino的A55型高速铣床采用电主轴和主轴贯通内冷却方式实现高速高功率输出,并使主轴始终保持低于箱体的温度。
机床机床必须具有足够高的刚度和最佳的阻尼特性,以防止切削时刀具颤振对工件表面质量产生不利影响:运动灵活,以适应进给轴的快速移动:要有高的动态特性,除了高的主轴转速和进给速度外,还要有高的加/减速度。
刀具夹紧技术应采用锥部与主轴端面同时接触的双定位刀柄。如德国的HSK空心刀柄。夹紧装置使铣刀刀柄与主轴很好地连接在一起必须保证在高速下刀具不发生窜动
5 高速加工对CAM软件的要求
高速加工有着不同于传统加工的特殊的加工工艺要求,故应用于高速加工的CAM 编程系统必须具有很高的计算编程速度,具有全程自动过切处理能力及自动刀柄干涉检查功能,具有进给率优化处理功能、待加工轨迹监控功能、刀具轨迹编辑优化功能、较强的插补功能、“加工残余分析”功能。
高速加工编程时应注意,由于残余量加工或清根加工是提高加工效率的重要手段,一般应采用多次加工或系列刀具从大到小分次加工,直至达到模具所需尺寸,不应用小刀一次加工完成。刀具应缓慢切入工件,下刀或行间过渡部分最好采用斜式下刀或圆弧下刀,不宜垂直下刀直接接近模具材料:同时,缓慢地从一个切削层进入另一个切削层比切出后再突然进入另一个切削层要好:其次,尽可能地保持稳定的切削参数,包括保持切削厚度、进给量和切削线速度的一致性:此外,当遇到某处切削深度有可能增加时,应降低进给速度,因为负载的变化会引起刀具的偏斜,从而降低加工精度、表面质量和缩短刀具寿命。这些对高速加工是否成功是至关重要的。
值得注意的是,不是所有CAM软件都能用于高速加工数控编程。在国外已有一些很成熟的适用于高速加工编程的软件包,如英国DelCAM公司的PowerMill软件模块,还有一些机床厂商专为高速加工开发的CAM软件,如Makino公司将它的FFAUT软件的FF加工模块集成到美国UGS公司的CAM软件中。国内相关的软件有北航海尔华正软件有限公司开发的CAXA-ME软件。
6 高速切削的应用
在高速加工中,不同工件材料和刀具直径要求的主轴转速与进给速度不一样。列举出了采用不同直径的TiAlN涂层球头立铣刀粗加工硬度不同的硬质钢时采用的主轴转速和进给速度。
机床的主轴转速N与刀具材料及切削速度和刀具尺寸有关。表2列举了使用直径为20mm不同材料的立铣刀在采用不同切削速度时所采用的主轴转速。
以注射模手机型腔模具加工为例,模具材料为HI3,硬度为50HRC,现用日本牧野HYPER5 机床进行加工,该机床主轴最高转速为32000r/min,最大进给速度60000mm/min。粗加工和半精加工时用?6mm 球头立铣刀,精加工时用?4mm 球头立铣刀,总的加工时间41min。各加工阶段所采用的加工参数和所用的加工时间如表3 所示。本例主要说明高速加工能缩短加工时间,提高了加工精度,减少抛光工作量或免去了抛光工序。
声明:本网站所收集的部分公开资料来源于互联网,转载的目的在于传递更多信息及用于网络分享,并不代表本站赞同其观点和对其真实性负责,也不构成任何其他建议。本站部分作品是由网友自主投稿和发布、编辑整理上传,对此类作品本站仅提供交流平台,不为其版权负责。如果您发现网站上所用视频、图片、文字如涉及作品版权问题,请第一时间告知,我们将根据您提供的证明材料确认版权并按国家标准支付稿酬或立即删除内容,以保证您的权益!联系电话:010-58612588 或 Email:editor@mmsonline.com.cn。
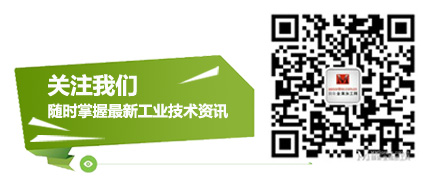
- 暂无反馈