航空发动机制造技术
发动机是飞行器的动力装置。这是因为它既要工作高度可靠,又要有尽可能小的重量。这就要求使用轻合金、合金钢和耐热合金制造形状复杂的整体或薄壁零件,要求零件加工有极高的精度,要求广泛采用热处理、表面处理和各种特殊的加工工艺。
飞行器的进步都与动力装置的进步密切相关。世界上第一架飞机就是从成功地采用一台8.8千瓦(12马力)活塞式汽油发动机开始的。1938~1942年涡轮喷气发动机的出现,为高速飞行奠定了基础。1930年制成了使用液氧的火箭发动机,为40年代导弹的研制成功创造了条件。
从制造角度来看,前期活塞式航空发动机与汽车、拖拉机用的一般内燃机的制造基本相似,现代航空航天发动机进一步要求提高推重比、减轻结构重量和提高寿命。这就使得发动机在结构型式、材料选用和制造技术方面与一般中型机械制造很不相同。发动机的制造包括零件的制造和加工、装配试车和质量控制三个主要方面。
1、零件的制造和加工
包括零件毛坯的制造、零件的外形加工以及赋予零件特定性能的热处理和表面处理。①毛坯精化:主要采用精密锻压、精密铸造和粉末冶金技术制造零件毛坯。采用精密锻压技术制造发动机的盘、轴、叶片等,可获得精确的毛坯外形。等温模锻和超塑性等温模锻用于锻造发动机中的高温合金和钛合金涡轮盘、压气机盘和整体涡轮毛坯。熔模铸造技术在发动机制造中发展很快,已用于制造切削余量小甚至无余量的空心涡轮叶片、整体涡轮和导向器以及钛合金零件。采用定向凝固技术制造的定向柱晶、定向共晶和单晶叶片,能承受更高的工作温度和应力,使高推重比发动机的制造有了重大突破。合金的超细粉末经热等静压可制成供超塑性等温模锻的坯料,也可直接制成外形和尺寸精确的零件毛坯。制造外形和尺寸精确的毛坯(毛坯精化),既节约贵重的金属材料,又减少切削加工工作量,提高生产率,降低生产成本。②切削加工:现代发动机制造中面临的问题是大量难切削的金属材料、复杂的型面和要求很高的精度与表面光洁度。因此需要采用新型刀具材料和刀具结构以及高效工艺方法。如利用强力磨削可一次磨出涡轮叶片的榫头齿形;利用高速拉削可一次切去压气机叶片榫头或涡轮盘榫槽的全部加工余量。切削加工所用的机床主要是专用机床和数控机床(见数控加工),这些机床应具有高的刚度和精度以及大的驱动功率。③钣金成形和焊接:现代发动机制造中,用钣金成形和焊接方法制造的零构件数量显著增加,如喷气发动机壳体、燃烧室、尾锥和气冷式板焊空心叶片等,制造工作量约占20%以上。这些零构件所用的材料为钛合金、耐热钢和高温合金等难成形材料,故在成形中广泛采用热成形、超塑性成形、强力旋压等工艺方法。为保证焊接质量,大量采用氩弧焊、电子束焊和真空钎焊。摩擦焊和扩散连接技术用以连接轴、盘等重要承力构件和异种材料(见焊接技术)。④特种加工:特种加工在发动机制造中是常规机械加工不可缺少的补充加工方法。其中以电加工和激光加工的发展最为迅速。在发动机的燃烧室、叶片和冷却管上均带有大量冷却小孔。这些孔不但数量众多、材料难切削,而且有些孔的形状特殊、深径比大,只能采用特种方法加工。例如,燃烧室上大量深度较浅的气膜冷却小孔可采用高生产率的激光打孔或电子束打孔。对一些孔径较大深径比也较大的小孔可采用电加工。⑤热处理和表面处理:飞行器发动机的所有零件都要经过热处理,使零件具有必要的性能,消除残余应力,稳定尺寸。除采用通用的热处理工艺和设备外,还采用真空热处理和在保护气氛中热处理。在化学热处理方面,除渗碳、渗氮外,渗金属和多元素共渗技术有了很大的发展。例如,在涡轮叶片表面进行铝-铬共渗或铝-硅共渗,可以显著提高零件的抗高温腐蚀性能。表面涂层技术在发动机制造中的主要作用是提高零件的耐磨性、耐蚀性和热稳定性,延长使用寿命。例如,在压气机风扇叶片凸台表面喷涂一层碳化钨涂层,可显著提高表面的耐磨性能;在燃烧室的表面涂敷高温陶瓷,可以显著提高零件的抗高温氧化和耐腐蚀的性能;在机匣的表面喷涂铝或塑料等用以控制间隙的涂层,可以保证机匣与相邻叶片之间的最小间隙尺寸。
2、装配试车
发动机的性能要求十分严格,它的空间结构又非常紧凑,故装配过程必须非常仔细。在装配过程中,不允许对装配零件进行整修,其配合精度完全靠机械加工精度和钳工调整来保证。如火箭发动机涡轮泵的端面密封需要使用光学平晶检查,并在装配后进行气密性检查,严防泄漏。高速转动的涡轮泵等部件装配后必须在精确度极高的动平衡机上仔细平衡。在装配前后,还须仔细清查装配零部件的数量,防止有多余的零件遗留在发动机内。一些精密部件(如活门部件)的装配和总装必须在清洁、防尘并有空调装置的厂房内进行。每台发动机第一次装配完毕后,必须先进行工厂试车,随后分解、清洗和严格检验。检查发动机零件在运行过程中有无磨损或性能不符合要求处,以便采取措施,消除隐患。经过检验合格的零件重新进行装配,再作检验性试车。试车性能全部合格后方能出厂。在成批生产的发动机中,还须定期抽检一台,模拟使用状态进行长期试车,以考验同批发动机的性能是否稳定可靠。上述试车时间均计入发动机的额定使用寿命内。
3、质量控制
在发动机制造中严格的质量控制贯穿于发动机制造的全过程,从原材料开始,经过毛坯制造、机械加工、热处理、表面处理、装配试车,直到包装运输、交付使用,每一工序都对质量要求及控制技术措施有明确的规定。在几何量的检测方面,关键是高精度、多尺寸检测和复杂型面的检测。以光学投影和数字显示技术为主要内容的现代化几何量检测技术,在发动机制造中获得普遍应用。多坐标数控测量机已成为重要的检测工具,大量用于检测形状复杂又多孔的机匣、壳体类零件和具有不同空间角度的弯管以及精密复杂的工艺装备。多点电子测量仪已用于叶片生产线;主动检验在高精度零件精加工工序和自动线中得到普遍应用。理化性能检测中的无损检测,如X射线探伤、超声探伤、磁粉探伤、荧光探伤、涡流探伤和激光全息摄影技术等,不仅用于发动机零部件的质量检查,而且也用于原材料和毛坯的质量检查。重要零件的毛坯要逐件检查。金相检验、室温和高温机械性能等破坏性检验方法,也用来对特别重要的零件作抽样检查。
声明:本网站所收集的部分公开资料来源于互联网,转载的目的在于传递更多信息及用于网络分享,并不代表本站赞同其观点和对其真实性负责,也不构成任何其他建议。本站部分作品是由网友自主投稿和发布、编辑整理上传,对此类作品本站仅提供交流平台,不为其版权负责。如果您发现网站上所用视频、图片、文字如涉及作品版权问题,请第一时间告知,我们将根据您提供的证明材料确认版权并按国家标准支付稿酬或立即删除内容,以保证您的权益!联系电话:010-58612588 或 Email:editor@mmsonline.com.cn。
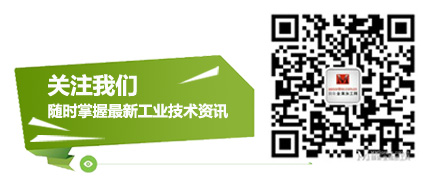
- 暂无反馈