上海制造世界顶级1.65万吨油压机 再次扬眉
“中国制造”再一次扬眉吐气,1.65万吨油压机的登场,既是提升制造业能级的奋力拼搏,也是装备业面向未来的大胆创新。
1.65万吨油压机在上海重型机械厂开锤运行,随着技术人员轻轻摆动操作杆,烧得透红的圆筒形巨大钢锭,像柔软的橡皮泥一般,被精确“捏”成了一件用于核电的大型铸件。
万吨压机在上海并非第一次登场。早在1962年,我国第一台万吨水压机在上海制成,为我国自力更生发展现代工业作出了贡献。
“1.65万吨油压机是一个浩大工程,仅成本就超过2.5亿元。”万吨压机工程负责人、上海电气集团副总裁、上重公司董事长吕亚臣告诉记者,造这样的“大家伙”,要突破的不仅是一个技术问题,更是一个思想解放的过程。
2004年底,当上重领导酝酿着再造一台万吨压机时,引发了一场热烈的思想碰撞。有人质疑:“我们不是有一台万吨压机了吗?虽"廉颇老矣",但还能运行,有必要投数亿元巨资再造一台吗?”有人担心:制造万吨压机,可能会需求不足导致空置,有可能血本无归。
当时的上重刚刚走出市场困境,对于一个关乎企业未来发展存亡的决定,谁也不敢妄下结论。然而,上重领导敏锐地嗅到了利好的宏观环境因素:国家确立“大力振兴装备制造业”的战略,重型装备制造业的机遇千载难逢。
以电力行业为例,30万千瓦机组在上世纪90年代已称得上“最大”,要锻造相关铸锻件,2500吨级压机已绰绰有余。但进入新世纪后,我国电力、冶金、石化、船舶等产业不断升级,发电机组从30万千瓦到100万千瓦、远洋船舶从几万吨到30万吨,大型锻铸件的需求缺口越来越大。而那台记录了上重人光荣与梦想的万吨水压机,已经“超龄服役”。工作时,压机动梁下压到什么位置、什么高度,基本要靠技术工人用肉眼“毛估估”,铸锻件精度无法保证;而由于“年事已高”,“老万吨”常常只能干两天歇三天。
另一方面,我国需要的大型锻铸件不得不大量依赖进口。上重公司党委书记周哲伟告诉记者:“由于国外企业具有垄断地位,制造速度是根据客人多少而定的。你只能排队等着,常常一个铸锻件要等上两年,十分被动。”
再造新的万吨压机势在必行。一条产业升级链在大家头脑中逐渐清晰起来:大吨位压机—大型铸件—大型装备—高水平的产业能级—世界领先。这根链条环环紧扣,成为上海装备产业突破发展瓶颈的必然选择!
充满挑战的制造过程
站在全新的1.65万吨油压机面前,83岁的万吨水压机副总设计师林宗棠掩饰不住心中的激动:“50年前,我从北京到上海,和同志们一起用了四年时间,设计建造成功了12000吨水压机。今天,上海电气重工集团,采用自主创新的现代化手段,只花了两年时间,就造出了1.65万吨自由锻造油压机,同样很不容易。”
相比水压机,油压机刚性强、稳定性好,压制力大、调节控制好,精度更是高出十几倍。在1.65万吨油压机现场总指挥王醒雷看来,制造过程异常艰辛,充满挑战。
油压机上下10多个大型零部件,每个都在100吨以上,其中最大的上梁净重362吨。光给一个“大家伙”翻个身要好几万元费用,起吊一下又要花数十万元,一旦返工就会增加巨大的成本浪费。吕亚臣立下一条规矩:“特大件的加工工艺要讨论并优化,大件加工不允许返工。”这一严格要求,使得在制造过程中,特大锻件从未发生返工现象,加工质量优良率达100%。
在压机安装过程中,要把300多吨重的上梁这顶“帽子”“戴”上4根立柱,就要解决准确定位的问题。因为16米高的立柱竖起来后,受重力影响,会出现外倾,难度很大。技术小组利用“四两拨千斤”的原理,做了一个细长的双头螺距调整拉杆,在立柱12米高度处拉了4根可以用于微调尺寸的拉杆,使立柱固定住。工人们通过调节4个螺杆孔的尺寸和对角线的尺寸,保证安装平面达到很高的精度。
吕亚臣说,万吨油压机的研制,锻炼了一支高素质的人才队伍,也捧回了10多项国家专利。经过18个月的自主创新,具有当代国际一流水平的1.65万吨自由锻造油压机便在上重厂房内拔地而起。
据了解,上重公司的大型锻件订单充足,已排到2010年以后,一年的销售额就达10亿元,5年就能收回1.65万吨油压机的投资,上重闵行基地也成为国内一流的大型铸锻件制造中心,进入发展快车道。
声明:本网站所收集的部分公开资料来源于互联网,转载的目的在于传递更多信息及用于网络分享,并不代表本站赞同其观点和对其真实性负责,也不构成任何其他建议。本站部分作品是由网友自主投稿和发布、编辑整理上传,对此类作品本站仅提供交流平台,不为其版权负责。如果您发现网站上所用视频、图片、文字如涉及作品版权问题,请第一时间告知,我们将根据您提供的证明材料确认版权并按国家标准支付稿酬或立即删除内容,以保证您的权益!联系电话:010-58612588 或 Email:editor@mmsonline.com.cn。
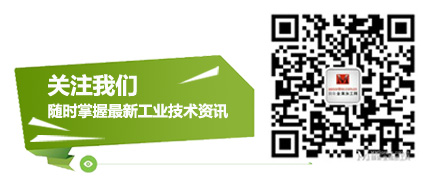
- 暂无反馈