世界造船市场仍呈下降趋势
装备工业基础零部件是指轴承、液压件、气动元件、密封件、齿轮、弹簧、粉末冶金件、传动连接件、联传动件、紧固件及模具等,在装备工业发展中具有举足轻重的地位,同时也是制约装备制造业发展的瓶颈。
历史上,我国基础零部件的发展经历了两次加速期,一是20世纪80年代初,通过引进消化吸收国外先进技术,使得基础零部件行业填补了空白,整体水平得到明显提升;二是20世纪90年代初,国务院办公厅下发《关于振兴特定基础机械和基础件若干措施意见》(国办发[1992]55号文),将轴承、液压、气动及标准件等基础零部件作为发展重点,全面推进了装备工业基础零部件发展。
目前我国基础零部件门类基本齐全,研发与生产体系基本形成,其中轴承产品规格已由1999年的39000种增加到2005年的66000多种,"神州系列"、"嫦娥一号"等国防重大装备配套轴承完全实现自主化;液压气动密封件基本可以满足国内主机配套和扩大出口的要求,其中液压产品产值首次迈进世界前三位。
但是,我国装备工业基础零部件仍存在产品档次低、可靠性差、寿命短的突出问题。工程机械需要的高压泵阀、盾构机和风电需要的轴承等全部依赖进口,液压气动元件仅有1350种、8000个规格,不足日本一家公司的1/5;铁路客车轴承寿命仅为进口同类产品的1/3~1/4。据统计,在每年进口的机电大宗商品中,基础零部件占到76%以上,国产装备70%的利润被进口零部件吃掉。基础零部件行业总体上处于低水平产品过剩、高水平产品不足、尖端产品短缺的状况,严重制约了我国装备工业发展,其主要原因:
一是自主创新能力严重不足,我国基础零部件行业存在"两弱两少"的问题,即基础理论研究弱,参与国际标准制订力度弱,原创技术少,专利产品少,设计和制造技术基本上是模仿。行业内没有一家国家级的工程技术研究中心,研究力量薄弱。与国外先进水平相比,研发周期是国外同类产品的2~3倍,新产品贡献率为国外的十分之一,总体技术水平落后15年以上。自主创新投入少且分散,我国基础零部件行业大都是中小企业,用于科研开发及新产品研制的资金,仅相当于国际知名公司的零头,全行业每年R&D投入只有销售收入的1%~2%。
二是产业集中度低,由于装备工业基础零部件行业进入技术门槛较低,大量粗放式的、达不到经济规模的小型企业不断涌现。基础零部件企业普遍规模小、缺乏市场竞争力,仅瑞典斯凯孚公司一家企业的销售额相当于我国近千家轴承企业销售额的总和,我国轴承工业四家最大企业的市场集中度为25%,而日本则达到90%。
三是制造技术和工艺装备发展缓慢,加工设备数控率和自动化水平低。大多数企业老旧设备占到80%以上。对基础件寿命和可靠性至关重要的先进热处理、表面处理、试验检测等工艺和装备缺乏,造成工序能力指数低,一致性差,产品加工尺寸离散度大,产品内在质量不稳定,严重影响了基础零部件的精度、性能、寿命和可靠性。
四是人员素质亟待提升,基础零部件行业人才培养体系不健全,不仅高技术人才缺乏,同时也没有建立起一支门类齐全、结构合理、掌握现代机电技术的技术工人队伍,专业技术人员尤其是工程技术人员总量不足。
为了彻底扭转装备工业基础零部件落后局面,提高自主创新能力和整体竞争力,业内外专家一致提出应尽快实施装备工业基础零部件振兴战略,集中力量突破关键技术,实施基础零部件专项工程;建设行业共性技术研发平台;建立主机与基础零部件企业的长期战略同盟关系;加强技术改造,完成产业技术升级;通过兼并重组做强做大基础零部件企业;研究制订税收优惠政策,促进基础零部件良性发展。
2009年2月4日,国务院第48次常务会议原则通过的《装备制造业调整和振兴规划》,明确提出了整机发展与基础配套水平提升相结合的基本原则,充分体现出国家振兴基础零部件工业的坚强决心,装备工业基础零部件正迎来历史上难得的发展机遇。
声明:本网站所收集的部分公开资料来源于互联网,转载的目的在于传递更多信息及用于网络分享,并不代表本站赞同其观点和对其真实性负责,也不构成任何其他建议。本站部分作品是由网友自主投稿和发布、编辑整理上传,对此类作品本站仅提供交流平台,不为其版权负责。如果您发现网站上所用视频、图片、文字如涉及作品版权问题,请第一时间告知,我们将根据您提供的证明材料确认版权并按国家标准支付稿酬或立即删除内容,以保证您的权益!联系电话:010-58612588 或 Email:editor@mmsonline.com.cn。
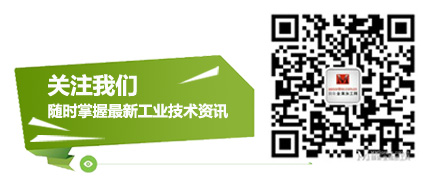
- 暂无反馈