机器视觉的用武之地--现代汽车制造业
随着其优越性的逐渐凸显,该技术已在包括汽车制造业在内的批量生产企业中获得越来越多的运用,应用前景广阔。自上世纪90年代初作为一项新技术进入实用阶段以来,机器视觉经过10多年的完善和发展,应用领域已日趋扩大。其在发达工业国家的应用较为普及,尤其在半导体和电子行业,约占总体应用的40~50%。而在国内,机器视觉产品的推出和应用尚处于起步期。
机器视觉是利用图像摄取装置(分CCD和CMOS两种),将目标转换成图像信号,传送给专用的处理系统后,根据像素分布和亮度、颜色等信息,转变成数字化信号;图像系统通过对这些信号进行各种运算,抽取出目标的特徵,进而根据判别的结果来完成各种运作。它具有非接触、高速度、工作范围大、获得信息丰富等优点。因其易于实现信息集成,故也成为制造业信息化中的一项基础技术。
机器视觉可用于标志识别、工况监视、产品(零部件)检验和质量控制等领域,对提高生产效率和自动化程度发挥很大作用。从技术层面看,机器视觉的主要功能可归纳为两项,即辨识和检测。
辨识功能的应用
辨识,亦称自动识别。相对而言,现代汽车制造业对机器视觉的辨识功能开发、利用最多。由此带来了制造过程柔性化程度的提高,加工可靠性和产品可追溯性的强化。
1.识别、读码、可追溯性
随着国家汽车召回制度的出台,如何有效地实现产品的可追溯性已成当务之急。相比用于商品识别的条形码,二维码包含信息更多,于是,企业进一步采取为重要零部件打上二维码的方式,将其包含的件号、批次等重要质量信息,经读数头识别采集后送至中央监控室的服务器。
然后,再结合各总成和整车上的条形码,一旦有需要,就可方便地查询,迅速、准确地进行针对性的质量追溯。而读数头对二维码的解读,正是利用了机器视觉的图像识别功能。
此外,通过读取工件上的二维码,还可控制生产操作和作业过程。例如,发动机缸体的轴承档与压入的轴瓦,采用的是选择装配方式,即两者都按测量结果进行分组(一般分3~5组),然后一一对应地进行压装。为了提高生产效率和杜绝错装,在成品缸体所打的二维码中,包含了第1~5轴瓦档(若为四缸发动机)的组别信息。
当工件在发动机装配线上移至某一工位时,设置的读数头即自动读码,工位外侧根据组数有3~5排盛放不同组别的轴瓦槽,前部有一指示灯。按1~5的压装顺序,操作工人根据指示灯提示,取出对应的轴瓦放入轴承档,显然,代表不同组别的指示灯的先后闪烁取决于读取二维码中相关信息后发出的控制信号。
2.提高作业的可靠性
为防止批量生产条件下作业工程(如:汽车发动机的装配工序)出现诸如零件错装/漏装,安装不到位及其他问题,必须提高作业的可靠性。建立在机器视觉辨识功能基础上的各种有针对性的自动识别系统,对提高作业可靠性相当有效。以下举2个典型案例。
1. 活塞-连杆组件在缸体内的装配
该自动识别系统的主要环节为:首先判断缸体是否已到位,并做好准备,其方法是探测缸体上缘(准确到位的标志),如果未发现该特徵部分,即发出报警信号。然后,对以下3项内容进行自动识别:1.活塞的有无;2.活塞位置的正确性(确切地讲是“周向方位”);3.活塞顶部表面的标识和字符(用于表明型号、选配时的组别及其它相关含义)与安装的缸体是否一致。
整个识别过程如下:发动机被翻转、装入活塞,输送系统使发动机随托盘向自动识别工位移动;当发动机即将到达时,先由二维码读数头验明其“身份”,然后发信号给PLC;一旦发动机到达自动识别工位,接近开关触发,PLC向机器视觉系统发出工作指令。如果活塞已安放在缸体内,其标识和字符与要求的型号、组别等完全一致,且装配正确、即“周向方位”在规定范围内,则视觉系统发信给PLC,令发动机流向下一工位。
如果活塞装配有错,则视觉系统提示PLC,并通过人机界面报警,显示屏将指示哪一缸的活塞装配有误以及属何种错误。操作者确认识别的结果后,通过人机界面向PLC发出指令,并且将发动机直接输送到返修区域进行返修。整个检测过程全部自动完成,只是在出现装配错误、发出报警时才由人工干预。
关于活塞位置的正确性,即“周向方位”的含义,如图1。在活塞底部(白色形象)的上方有个箭头,它必须位于图示位置,即处于与被安放的缸体(黑色形象)4个缸孔的中心线相一致的状态。活塞置于机器视觉探头之下时,通过一个圆框来判别箭头是否处在正确位置。
图1 活塞安放位置正确性的识别
2. 汽车车灯出厂前检验
各种车用灯具的日产量往往高达几千只。产品出厂前的检验一般包括判别2个螺丝的定向,测定拧入深度(要求精度达到0.1mm),并要求检查塑料垫圈、挡水片,以及垫片是否安装正确,还要求记录刻印在塑料座上的产品型号。
为此,采取了拥有4个摄像头的机器视觉系统,它们均设置在装配线上方,前2个摄像头检查螺丝的定向及拧入深度,第3台检查垫圈,挡水片,垫片等零件,第4台则读取零件型号。
4台摄像头所读取的图像送往1台PC进行处理判断并显示结果。为避免外界杂光干扰,该系统采用LED 照明装置。在这套机器视觉检测系统投用之前,企业每班需要2名检验员,每件检验耗时30秒,且有较大误差。采用后则不再需要专职检验员,检验速度大大提高,每件仅耗时5.5秒,差错率也降至零。
3.提高制造过程的柔性
现代汽车制造业,特别是轿车企业,其发展方向是采用多品种、柔性化的混线生产模式,而工件识别技术就是实现这种生产模式的一个重要环节,下面试举例说明。 为了在一条自动线上同时生产属于2种发动机的4种不同凸轮轴,采取了在工件指定的二档轴颈间制作标志的方法,标志是事先加工在轴间的1~4道环带,分别代表4种类型的凸轮轴,图2是其中的2种。
图2 带识别标志的工件
在工件进入某道工序(如凸轮轴的最终检测)之前,线上所设置的光电视觉传感器将通过读取上述标志,正确地对工件进行识别(如图3),然后发出相应的控制信号,以执行不同的工作程序。譬如,当图2中的凸轮轴在进入终检工位的前两个工位时,综合测量机就会根据收到的指令,调用不同的程序,以对该工件进行正确检测。
图3 视觉系统对工件的识别
检测功能的应用
检测是机器视觉的另一个重要应用领域,其与“辨识”的主要区别就是前者为定量,而后者为定性。检测功能可表现为多种形态的工作模式,适用于批量生产条件下,尤其是现代汽车制造业中不同场合的需要。
1.精密测量
应用机器视觉进行精密测量,建立在对被测对象图像的边缘检测的基础之上,如图4所示。检测系统主要由光学系统、CCD摄像头和计算机处理系统(图中未标示)等组成。
图4 测量系统工作示意图
由光源发出的平行光束照射到被测对象的检测部位上,其边缘轮廓经过显微光学镜组成像在摄像机的面阵CCD像面上,经计算机进行图像处理后获得被测对象边缘轮廓的位置。如果使被测对象产生位移,再次测量其边缘轮廓位置,则两次位置之差便是位移量。显然,若被测对象的两条平行的边缘轮廓能处于同一幅图像内,则其两者位置之差即为相应尺寸。
上述系统特别适合对大批量生产情况下工件的在线检测,尤其是在被测对象尺寸较小、形状比较简单时,其优越性更加突出。汽车电子产品中的接插件就是一个典型例子,它们的生产效率和成品尺寸精度都较高,前者可达到每分钟数百件,而后者多数为0.01mm的数量级。
一般情况下,工件的质量缺陷包括插脚的变形或扭曲、多余的金属粘附(金属碎屑)等,均反映为外形尺寸的误差。当采用图4所示系统进行测量时,由于零件(插脚)形成的图像与其明亮背景之间具有强烈对比,呈现出清晰的剪影效果。这就为准确测量被检对象的尺寸和轮廓(形状)特徵创造了条件。
图5显示了一部分冲压成形的插脚随着金属输送带通过检测工位时产生的典型背光图像。其中,插脚A发生了扭曲,插脚B上粘附着多余的金属,插脚C断面尺寸(宽)不合格——这些都属于常见的质量缺陷。
图5 典型的背光检测图像
用机器视觉进行精密测量的另一个实例是刀具预调测量仪。传统的检测方式是光学投影和光栅数显表相结合,前者用于瞄准定位,而后者用于测量、读数。整个过程需较多的人工参与,对操作人员要求高,效率却并不高。
几年前诞生的新颖刀具预调测量仪,将机器视觉、光栅技术、计算机软硬件、自动控制技术等有机结合,无论在测量精度、操作方便和工作效率上都有了革命性的提高。其主要原因就是以机器视觉替代了传统的光学投影,彻底改变了原有工作模式。
在这种新颖仪器中,作为运动导轨的Z轴、X轴和C(回转)轴内,分别装有直线光栅和圆光栅,被测刀具沿转台中心线、即C轴安装。机器视觉传感器位于叉形支架两侧,也即,跨越转台的中心线。支架的一端安放光源,另一端是摄像头,被测刀具的图像由摄像头读取。
2.工件表面缺陷检测
工件表面缺陷,比如连杆大小头结合面的破口缺损是在制造过程中形成的。迄今为止,在批量生产的汽车、摩托车、内燃机等行业,对表面缺陷的探测基本都是人工目测方式。此法不但效率低、劳动强度大,且难以准确执行工艺标准中规定的定量评定,影响了对产品质量的有效监控。
以连杆大头孔结合面的爆口为例,其评定标准的具体要求如下:1)破口面积小于3mm2, 2 )破口任一方向的线性长度小于2.5mm。只要符合上述一个条件,就将判定不合格而被剔除。
必须指出,与以上精密测量中机器视觉系统采用的透射方式(又称“背光” 方式)不同,表面缺陷探测需采取反射方式。此时,系统通过一个方形框式LED漫反射光源照亮待检测工件的破口区域,光线照射到对象表面后,反射到摄像头内的光电耦合CCD元件上,即转化成对应的电量信号,图像处理系统根据电量信号对得到的图像进行分析和计算,最终得到所需数据。
如前所述,CCD元件可理解为一个由感光像素组成的点阵。其每个像素都一一对应了对象的二维图像特徵,即通过对像素点成像结果的分析可间接分析对象的图像特徵。比如通过对二值化图像中的成像像素个数的计算,便能得到相应对象的长度值和面积值。
图6 检测系统组成
以连杆结合面爆口为例,根据被测对象的特徵(工件形状、被测部位)和要求,需分别检测互为15°夹角的A-B-C 3个(连杆侧面的)破口面,最终以3个检测结果中的最大值作为破口的真实值,进行判断并输出结果。据此,组成了如图6所示的检测系统,它主要包括:
1. CCD摄像头;用于采集破口图像并转换成数字图像信号。
2. LED光源;用于提供稳定、均匀的照明,保证取像质量。
3. 图像处理单元;其可根据需要,对采集到的图像进行处理、分析,同时把分析结果和图像系统的状态信息通过RS232接口传向PLC。系统使用松下的MultiCheckerV110嵌入式图像处理系统,集图像处理和输出为一体。嵌入式图像处理系统的特点是处理器体积小(8.4×4.0×12cm)功耗低(24VDC,0.7A),且环境适应性好,能在环境温度50℃的条件下连续工作。
4. PLC;它控制整个检测系统各项功能的执行,同时也对图像处理单元传过来的数据进行校验和判断。本系统选用西门子公司的S7-226MX。
5. 监示器。它作为人机交互界面,显示图像处理系统的状态和数据分析结果。
3.机器视觉在检测自由曲面中的应用
汽车车身以及其覆盖件(焊接件、冲压件等)大多呈自由曲面状,多年来,对它们的检测主要是采用坐标测量机。为提高测量效率,尤其是考虑到强化对生产过程的监控,自上世纪九十年代中期起,利用先进的光学测量系统在现场实施在线检测的方式逐渐兴起,而这种新兴测量装置正是激光传感器和机器视觉相结合的产物。
光学测量装置的工作原理是三角测量法。由半导体激光器发出的光经过聚焦,照射在被测物表面,其反射光通过成像透镜,成像于图像摄取装置的CCD面阵上。依据三角测量的原理,当被测表面偏离基准面时,在图像接受器件上的成像点也将产生相应偏离,据此能求得被测工件表面不同部位的实际值。
上述激光视觉测量经过多年发展,已从早期主要用于一维尺寸和距离的检测,进入到三维测量,但其工作原理仍为三角测量法。
当然,相比利用三坐标测量机检测工件的自由曲面,激光视觉测量的重复性R和精度AC要低得多。正因为此,它们主要用于在线检测,通过高效、快速的100%测量和对实测值进行统计分析,实现对动态生产过程的质量监控。
声明:本网站所收集的部分公开资料来源于互联网,转载的目的在于传递更多信息及用于网络分享,并不代表本站赞同其观点和对其真实性负责,也不构成任何其他建议。本站部分作品是由网友自主投稿和发布、编辑整理上传,对此类作品本站仅提供交流平台,不为其版权负责。如果您发现网站上所用视频、图片、文字如涉及作品版权问题,请第一时间告知,我们将根据您提供的证明材料确认版权并按国家标准支付稿酬或立即删除内容,以保证您的权益!联系电话:010-58612588 或 Email:editor@mmsonline.com.cn。
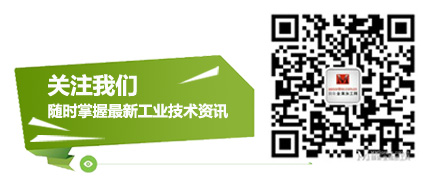
- 暂无反馈