数控技术领域切削加工的数字化测量技术与分析
【编者按】随着制造技术的快速发展,数控高速切削数控技术作为一种先进的制造技术,其研究制造的工艺也在不断的创新和提高,在操作中必须保障高效的加工质量.也要实现加工数控切削的高效率。本文首先介绍了数控切削加工技术.然后列数字化测量技术的基本原理以及刀具的检测技术进行了探讨,最后对数控切削加工领域数字化测量技术的发展趋势做出了评价。
0 引言
由于我国汽车、能源等交通运输等苇要领域应用的一些重要重大的装备材料在制造E有一定的要求和难度,冈此数控高速切削技术作为一项先进的制造技术在近几十年快速发展,严格高效的数字化切削加T技术的开发巳成为制造业所关注的再点。刀具技术也在数控高速切削技术发展过程中起着关键的作用,确保了在严格的数控切削技术中切削加工质量的合格和技术的高效性、精密性。
1 数控切削加工工艺
1.1数控高速切i削加工新工艺
中国是个制造人陶,我们只有掌握先进的核心制造技术,才能防止在先进的制造队伍中掉队,数控切削加工作为制造技术的}要上艺,也是汽车工业、能源业和航空航天制造业装备材料的主要技术。高速切削技术是经过对高性能刀具材料及刀具设计、制造技术、高精度测肇测试技术进行综合测试研究而成的。在制造行业新技术材料的需求度日益增多,开发高速切削新工艺才是推进制造技术前进的必要前提。高速切削技术的开发是一项很有挑战的突破,所以很值得继续探索开发来加快人类社会的进步。
1.2 高速数控切削加工的优越性
高速切削技术足一种先进的制造技术,超高速的切削加工技术切削速度的大幅度提高,不仅能提高效率和质量还能降低加工成本,使得零件的加工精度和质量得到更高程度的提高。超高速数控切削超越了一般的切削技术,应用了纳米等先进技术,突出了明缸的优越性。1)高精度的加工:高速切削的切削力比一般的切削度要小,在加工方面粗糙度大大降低,切削的频率高使得加工的过程更加平稳,切削能达到更高的精度。2)高效的加工效率:高速的切削技术的应用,保持切削时间不变,可减少进刀量,增加切肖Ⅱ次数,降低切削力,从而提高表面光洁度,使通过手工抛光的部分全部省去或减少到最低的工作量,从而切削速度和频率都大幅度的加快提高,加工表面的受热时间短,不会由于温升导致热变形,所以在一定时间内零件材料的加工效率也会大幅度的提高。3)高效环保:高速切削时,由于速度频率高效,减少了装卸、搬运的时间,加工时间大大缩短,延长了设备的使用寿命,减少,能源的消耗同时减少了污染。
1.3 数控高速切削技术的应用领域研究
高速切削技术高效的优越特点广泛运用在各行的制造业领域,数控高速切削技术的虚用将产生巨大的经济效益。在航天航卒和汽车业,由于数控高速切削速度和频率都大幅度的加快提高,加快了零件材料的切除效率。采用高速数控切削技术,提高了连杆模具加工的速度,采用了非常小的切削深度,延长了模具的寿命,可直接较小直径的刀具进行精细加工,简化了连杆模具的加工工序。在模具的高速精加工中,在每次切入、切出工件时,采用圆弧或曲线转接,避免采用直线转接,以保持切削过程的平稳性,以获得最佳加工表面质量。
2 切削加工领域的数字化测量技术
2.1 数控切削加工中数字化测量技术的基本原理
先进的数控切削加工技术离不开标准的数字化测量技术,数字化测鼍首先要确定零件中刀具起始点的位置,再通过精密的仪器来确定坐标系中零件的具体位置。数控加工工艺比一般的加工工艺有一定的难度,前提条件也有很多,比如说刀具的正确选择,合理的加工工艺路线和切削方法。还要考虑数控加工零件的加工具体位置。从刀具的设计制造以及刀具的出厂,数字化的测量技术都起着至关重要作用。先进的数控切削刀具是切削过程的关键,因此,数控加工设计的过程必须严格谨慎,尽最减少错误的发生。在数控加工全过程中,有多种数控切削工艺方案进行选择,可以选择零件的加工部位作为切削的主要线路,也可以选择刀具作为主线来安排加工,因此数控加工相比于传统的加工工艺更具有多样性。由于数控加工的自动化程度比普通机械的加工技术高,所以,必须严格检测数控加工工艺确保生产全过程的安全和质量的保障。
2.2 数控高速切削对刀具材料的要求
数控高速切削时,由于切削时产生了高强度的热量,所以刀具所受的磨损很高,因此,数控高速切削时使用的刀具材料要经过严格的选择制造才能符合切削时所遇到的各种难度。刀具的材料最主要要具有高强度、高硬度和强抗热冲击能力,除此之外还要考虑刀具的加工工艺质量和使用寿命。但是满足这些条件的刀具在制造方面具有很高的难度,所以应尽量满足刀具具有较好的抗冲击力,可以应用一些稀有的材料,比如高强度钢加工制造的刀具具有更高的强度和韧性。采用钛合金等材料,高镁度的钛合金,在切削加工时由于其强度高耐蚀性好,耐热性很高,所以也在发动机等机体上广泛应用。它抗冲击力强度适中,同时也避免了刀具磨损严霞和温度过高的现象反而延误加工。复合材料可以广泛运于航空航天零件制造业,复合材料代管r很多传统的材料,面材的强度高具有很强的刚度和厚度,因此很容易适波多种环境的变换。
2.3 数控刀具涂层检测技术
由于涂层可以改变切削刀刃上整个切鹏的成形过程,因此,刀具涂层对刀具性能的改善和加工技术的进步起着重要作用,致使涂层刀具成为现代刀具的标志。通过刀具涂层,可以减少刀具磨损、提高切削速度、减少摩擦热、提高加工表面质量、减少对硬质合金刀体的热传导和提高刀具耐用度等,使涂层刀具在切削加工得到广泛应用,特别枉干切削和硬加丁中起着十分重要的作用。刀具涂层检测刀具切削性能和效率的荚键。为了提高刀具的切削效率,提高刀具的性能,降低成本,提高材料的利用率。新的刀具涂层材料不断被研发。刀具的涂层前阶段主要应用物理涂屠。物理涂层工作环境良好,能保持刀具良好的切削性能。近年来在传统的涂层基础上,有了高温红硬性更好的新涂层,金刚石涂瑶也得到了快速的发展。纳米涂层结构在同样的涂层情况下可显著提高涂层性能。确定了切削刀具涂层的基本配置条件还要确保数控刀具的质量的高切削性能,所以数控测量仪器也占有同等重要的地位。涂层技术对数控刀具的发展起了巨大的促进作用。刀具经过涂层后可大幅度地延长使用寿命,随着涂层工艺的不断创新和研发,经过涂层的刀具可以有效的提高切削效率,降低生产成本和刀具的加工制造成本。
3 切削加工领域的数字化测量技术的发展趋势
3.1 测量技术的进一步发展
随着制造水平的提高,为了实现数控切削的高效率,达到测量技术的主要指标,推动测量的进一步发展,必须提高测量的效率。随着多种测量技术的飞快发展,选择正确的测量技术,尤其对于机床的性能上发挥雨要的作用,要求测蕈组建具有极高的策略精度,减少细小的误差,同时不能减少驱动系统的分辨率。数字化测鼍技术应在测镀水平测量精度方面朝肴高效精准的方向发展,将测罐的范围扩大,从单方面到多寿面测肇发展,应用光笔测量仪可以移动到离工件很近的地方进行测蹙,在一些零件工装、夹具的现场测罐,由于工件庞大不易移动,结构复杂,隐藏点过多,所以使用光笔测肇仪,既节省看作业时间,又提高了测毓精度,提高了生产效率。在此基础上还要采用高效精密的三维测毓仪器米进一步完藩测毓标准。第-三代镭射测景技术因其独特的机械式防护系统可完杜绝切削液和粉尘切屑侵入光学系统,可以在最恶劣的工作环境下工作,在加工过程中不用清洁工作台就可以实现
在线的测量,这样不仅节省了大量生产时间,还提高了加工效率。
3.2 创新技术的发展
制造业的强盛与否,是衡量一个国家是否强盛的重要标准,要保持制造业强盛不衰,其关键就是技术不断创新。为了提高数控切削技术的高效发展,使得产品材料不断得到优化,新产品的开发使得切削技术面临巨大的挑战。近几年,一些耐磨的复合材料一直都是切削加工的障碍,长时问的切削,会降低产品的生产效率,缩短了刀具的寿命,新工程材料的不断开发研制,也提高了切削的技术。各行业在制造发动机传动器等零件的时候,采用新材料比如硅铝合金与高强度,这样能减少了汽车的能耗,开发创新加工技术,能从根本上解决数控切削数字化测量的加工难度。
3.3 推动制造业的发展
随着产品多样化的发展,当今制造业只有加快更新的步伐,在产品的结构零件功能}:做出创新,才能适应制造产品的趋势化,数控刀具数字化测量仪器领域在清洁能源核电制造业得到了快速发展。发电设备上一些关键的零件经过高效的切削加工,一些高强度高硬度的刀具克服了一切强度高的村料切削,先进的数字化测量技术可以检测发电设备零件的加工检渊,高精度、大规格风电加速传动箱齿轮成形加工测量,也在一定程度上反映了先进切削技术及先进数控刀具,备受工具制造行业关注。还有一些大的工具厂根据眼的的形势制定了发展的目标,自行研制了先进的超硬刀具数控制造装备和技术,先进数控刀具/刀片涂层装备和技术,以及高速钢热处理技术等等。装备制造业也对数控切削的工具有很大的需求,冈为需求的不同,所采用可转位刀片基体材质、涂层要求、刀片几何参数、整体刀具结构设计等都会有很大差异,然而硬切削、超精切削以及包括复合材料在内的新型材料切削,解决了一部分难题,进一步推动了超硬刀具的需求和发展。以齿轮滚刀、插齿刀作为代表的高效高性能精密复杂数控刀具,在汽车、船舶、航空、风电核电、铁路、工程机械等行业的齿轮传动装置制造中受到广泛的使用。
4 结束语
为了跟上国际生产业的快速发展,尽早赶上国外的先进水平,提高零件的加工率,数控高速切削技术作为一项先进的制造技术,一直值得我们去探寻和开发,我们一定要全方面掌握现代化的数字化测量技术,通过精确的测量,依据实际情况制定合理的数控切削程序,通过一个不断修改完善的过程,这样既可以提高材料的加工质量和水平。也可以达到逐步各项成果标准化、系列化的效果,加快经济的发展和提高人民的生活水平质量。
声明:本网站所收集的部分公开资料来源于互联网,转载的目的在于传递更多信息及用于网络分享,并不代表本站赞同其观点和对其真实性负责,也不构成任何其他建议。本站部分作品是由网友自主投稿和发布、编辑整理上传,对此类作品本站仅提供交流平台,不为其版权负责。如果您发现网站上所用视频、图片、文字如涉及作品版权问题,请第一时间告知,我们将根据您提供的证明材料确认版权并按国家标准支付稿酬或立即删除内容,以保证您的权益!联系电话:010-58612588 或 Email:editor@mmsonline.com.cn。
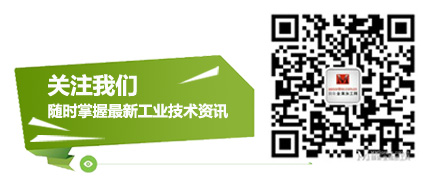
- 暂无反馈