高速切削技术在汽车轮胎模具制造中的应用
随着全球公路建设和世界汽车工业飞跃式的发展,汽车的类型越多,行驶速度也越来越快,汽车对轮胎的性能要求在不断提升,轮胎结构也在不断改进,花纹样式更是持续更新,因此对轮胎模具特别是高精密子午线轮胎模具的质量要求越来越严格。对于精密汽车子午线轮胎而言,轮胎花纹的加工精度只要差一点,将直接影响到轮胎的性能。因此轮胎模具的制造必须满足轮胎的高精度要求,这将使模具制造商面临着前所未有的考验。
轮胎模具在模具大家族中个性化较强,是一种“动态”模具。不同的规格型号、不同的用途、不同的路面状况、不同的配套车辆、不同的气候环境、不同的性能要求对轮胎的花纹设计和加工提出迥然不同的要求,因此轮胎模具的设计和加工有它独特的一面,它的技术含量一点不亚于金属冲压模具,其加工精度特别是子午线轮胎模具的型腔花纹的加工精度,每一处的精度都可能关系到轮胎的使用性能,如抓地性能、动平衡性能、静平衡性能、均匀性、散热性、转弯性能、防滑性能、噪音度、排水性及气密性等,因此轮胎模具在制造技术上也相应具有一些独特的工艺技术。
国内外轮胎模具加工技术比较
目前国内外轮胎模具的花纹加工方法总体上来讲有下面几种:贴花、EDM(电火花腐蚀加工)、精密铸造、专机数控雕刻。
1.贴花
贴花工艺是在设计模具时将轮胎花纹筋条和模具本体分开,不按常规那样加工一体,而是沿着模具本体的胎顶曲面粘贴或镶嵌花纹筋条,使之形成整体的一种工艺。
这种工艺技术在一定范围内方法简单、容易操作,加工周期也短,特别是工程车轮胎模具比较适合。但是存在镶嵌间隙,容易在轮胎产生局部胶边,影响轮胎外观,另外也由于改变了模具的整体结构强度,不适合于壁厚较薄的模具,对于复杂花纹更不适合。
由于该技术的极限性,因此目前国内使用该工艺技术的模具厂家并不多,国际上也不多见。
2.电火花加工
轮胎模具的电火花加工位置就是与轮胎花纹相对应的部位,其结构复杂多变,花纹的结构往往有呈现空间三维扭曲、多角度、多方向、尺寸大小不一、深浅不一等特点。
在轮胎模具行业中,电火花加工只是一般的成形加工,再经过钳工抛光,最终由人为因素决定模具质量。在加工轮胎花纹过程中,电火花工艺存在以下的问题:
(1)轮胎模具花纹复杂多变,结构奇特,很多结构是不能电火花一次性加工出来的,电极的分割需要有很好的技巧,否则将形成因花纹结构倒扣而过切,直接影响轮胎花纹的形状和精度。
(2)电火花加工后表面往往显得粗糙,需要人工研磨抛光,效率低,表面粗糙度也难以达到均匀一致,满足不了精度要求,质量不稳定,影响轮胎表面质量。
(3)电火花加工本身也能够保证轮胎花纹表面的粗糙度和精度,但一般是极限于较慢速的加工,其效率满足不了市场需求。而按照目前的工艺水平,采用高速电火花加工,则不能很好控制表面质量。
(4)花纹整圈电火花加工后再切割成块,因切割所产生的切割缝将直接影响轮胎模具内腔的圆跳动精度,同时对于生产管理来说,在机时间长,转序速度慢,直接影响交货期。
(5)一般来说,电火花加工工艺适用范围比较广,但是对于冬季轮胎来说,由于花纹结构十分复杂,而且钢片特别多,因此电火花加工就发挥不出其优点,特别是批量生产的时候。
综上所述,传统的电火花加工工艺已经变得跟不上市场要求的步伐,其在轮胎模具花纹加工中也将被逐步限制。
3.精密铸造
精密铸造工艺在轮胎模具制造中是最重要的制造技术之一,在零件的复杂性和材料适应性方面具有无可比拟的优势,但铸型的制造往往需要一个较长的周期,铸造工艺装备较多,成本较高,铸件的结构和尺寸的改变将会直接影响铸型的设计、制造、装配等较长和较复杂的工艺过程。
目前,精密铸造技术通常用于生产半钢轮胎模具,全球至少有90%以上的半钢子午线轮胎的生产采用精密铸造铝合金模具。由此可知,精密铸造技术在半钢子午线轮胎的生产中占有绝对主导的地位。
4.专机数控雕刻
这是一种采用专用数控雕刻机床来加工轮胎模具花纹的工艺。这种加工工艺是利用微机控制专用铣床进行四轴二联动或三联动,并根据预编程序进行自动刻花。数控雕刻工艺技术代替了传统的仿形雕刻技术,在某一程度上提高了轮胎模具的加工质量和加工效率。
由于专机数控雕刻所使用的机床其专用性很强,而且一般情况下采用三轴或四轴加工,其主轴转速能达到10 000r/min就已经算不错的了,一般情况只有几千转/ 分钟的转速。而且机床的联动性能也不是很优化,因此一般只能做到半精密加工,然后再配合电火花进行精密加工。同时,这种加工工艺要求花纹不能分块,而且需要整圈加工,因此这种加工工艺还有一定的局限性,不管从加工精度上还是加工效率上,都无法做到满足高等级性能轮胎模具特别是高等级性能的半钢丝子午线轮胎模具的要求。
高速切削技术在轮胎模具加工中的应用
轮胎影响着汽车诸多方面的性能,高精密的轮胎模具对于生产优质的轮胎尤为重要。高速切削加工技术应用于轮胎模具的生产中,不仅突显出其切削效率高、加工精度高、表面质量好的特点,而且也体现出其大大缩短了机械后加工、人工后加工和取样检验辅助工时的优势。
目前,随着技术性能要求的提升,汽车轮胎胎面的花纹图案变得愈加复杂和精致,原有的铸造模具和电火花加工模具已不能满足各种高精度轮胎制造的要求,取而代之的便是采用高速切削加工技术制造的高速直接雕刻模具。这种模具不仅精度高而且外观质量出色,完全消除了传统铸造和电加工过程中容易产生的潜在弊端。
高速切削(HSC)是近几年发展起来的一种集高效、优质和低耗于一身的先进制造工艺技术。高速切削是指采用超硬材料刀具和能实现高速运动的高精度、高自动化、柔性的设备,以极大地提高切削速度来达到提高材料切除率、加工精度和加工质量的现代制造技术。
高速加工技术用于制造模具,具有切削效率高、加工精度高和表面质量好等显著优势,还可以大大缩短机械后加工、人工后加工和取样检验辅助工时。
高速加工技术是一项先进的、不断发展的综合技术。要充分发挥高速加工技术的优势,除必须具备高速加工机床外,还必须综合应用高速加工刀具技术、高速加工工艺技术、高速加工CAD/CAM技术以及冷却润滑技术。随着高速加工技术的不断发展,高速加工的优势和作用将越来越明显。
轮胎模具行业的特点是单件小批量生产,因此,高速加工技术在轮胎模具行业的推广使用,有着非常巨大的发展潜力和发展空间。
高速雕刻技术的问题点主要是设备和刀具的成本高昂,一般企业不敢轻易投入。另外,对于花纹钢片比较多的、花纹锐角较尖的花纹图案,采用这种工艺技术也不大适合,理由是加工难度很大,且再小的刀具也不能加工出内尖角, 还是必须结合电火花加工来完成最后成形。
高速切削技术在轮胎模具加工中的要求
高速切削技术作为高效加工的重要手段之一应用于轮胎模具花纹的加工中,其技术含量相当高,涉及到多方面的内容,包括快速的规范的编程、多轴联动加工、细微刀具应用、标准化操作、并行加工等方面,可以减少了以往电火花加工和人工修整的工作量,还可以保证模具制造的高度一致性,确保模具精度,缩短加工周期,从而提高生产效率,实现高效加工。
随着汽车轮胎胎面的花纹图案变得愈加复杂和其技术要求变得越来越严格,高速切削加工已经被逐渐应用到轮胎模具花纹的雕刻加工中。而由于轮胎模具花纹具有明显不同于常规模具结构的特殊性,因此高速切削技术在轮胎模具加工中具有一定的技术要求。
1.对机床的要求
为了适应粗精加工、轻重切削和快速移动,同时保证高精度(重复定位精度±0.005mm),性能良好的机床是实现高速切削的关键因素。
(1)拥有高速主轴 既然是高速切削加工,机床的主轴能否达到真正的高速是满足高速切削加工的必备条件。因为轮胎模具的花纹加工中所使用的刀具比较细小,为了保刀具的切削效果以及对刀具给予最有效的保护,因此对主轴的要求很高,转速一般要求达到20 000~40 000r/min,甚至更高;进给速度达到40~80m/min;主轴功率一般为10~40kW。
(2)高速移动 高速切削加工并不仅仅是指机床的主轴拥有高速转动的功能,而且也应该包含高速移动功能,包括高速移动横梁、高速移动工作台等。
(3)良好的精度稳定性和抗振性能 为了减少模具在开粗时重切削所产生的振动以及在高速切过程各高速运动零部件产生的高热量等不利于保护机床使用及精度控制的因素,高速切削机床的床身等支持部件应具有很好的动刚度、静刚度、热刚度以及阻尼系数。因此对于高速切削加工的机床床身及其主要支撑部件应该采取质量高、刚性好的材料,以保证机床使用过程中精度稳定并消除因切削特别是重切削引起的振动。
(4)优秀的进给驱动系统 要满足高速切削机床的要求,除了必须拥有高速主轴之外,优秀的进给驱动系统也是关键条件。进给驱动系统应有很高的控制精度和响应速度,目前全数字伺服系统驱动已经成为高速切削机床所广泛使用的一种方法。
2.对刀具的要求
轮胎模具的花纹相当复杂多变,随着花纹的变化,需要的刀具形状和尺寸各不相同,刀具的直径最小可以达到0.5mm,甚至有些刀具的刃部结构是无法从市场采购到的,需要自己处理。不管如何,刀具在轮胎模具的高速切削加工中具有不可低估的作用,随着加工方式、工件材料以及刀具选择的变化,高速切削加工的速度会有很大变化。刀具的质量直接影响到轮胎模具的加工效率和加工质量,因此为了实现高速切削,必须对刀具提出要求。
(1)刀具材料选择 在加工时,必须根据工件材质来选用刀具的材料。虽然轮胎模具花纹部分的零件材料一般采用中低碳钢或铝合金材料,但由于所使用刀具直径较小,切削过程容易折断或崩裂,因此对刀具材料也要提出较高的要求,刀具应具有高强度、高韧性等性能,一般情况下可以有以下几种材料的刀具可选:金属陶瓷材料刀具、超细颗粒硬质合金刀具、表面涂层刀具如PVD高性能涂层刀具等。
(2)刀具结构选择 加工轮胎模具花纹时,刀具的结构选择除了应结合所使用机床的接口包括系统接口外,还应根据被轮胎模具花纹结构及加工工序来优化组合刀具材料、涂层和槽型功能,选定具有最佳切削效果的刀具结构。例如轮胎模具花纹筋条一般呈角度多变状,花纹筋根部要求无圆角且花纹筋末端经常有一些尖角需要处理,因此在选用刀具时既要考虑刀具可能如何避免或较少产生一定的R角,还要考虑选用坚韧耐磨的细微刀具,同时还要注意刀刃应利于在死角处如何排屑等问题。
(3)刀具装夹及防护 在高速切削过程中,必须加强刀具与夹紧装置的强度、刚度和稳定性,以保证在高转速下能够正常工作且安全可靠。注意刀具实际工作的转速,不超过刀具与刀柄夹紧装置制造厂家注明的允许最高转速。采用短锥空心刀柄代替传统刀柄,以提高刀具轴向和径向定位精度、轴向刚度,并具有过载保护作用
3.对工艺的要求
(1)为避免精密高速机床使用过于集中及精密机床过快受损,在处理加工工艺时如有可能可以考虑粗加工、半精加工和精加工分开,采用一般机床和精密机床相结合,以实现错位加工,缩短单件在机时间,同时保证机床常处于比较稳定的精加工状态。
(2)减少切削量,加大进给。传统的轮胎模具的机加工中,例如用铣刀进行侧面切削时,采用刀具直径进行全面加工的情况较多,但这样会造成切削热的传导与散发不充分,从而加速刀具磨损。在高速加工中,刀具在直径方向的进给量减小,而空转时间增加,从而赢得了充足的时间使切削热得到散发,由此可以减少刀具的磨损。
(3)快速清除切屑。高速切削过程中,工件受到挤压而被切削,这个过程中产生了大量的热量,据有关研究结果,高速切削后的热量一般按以下情况分配:约95%的热量集中在切屑上,2%的热量留在工件上,3%的热量在刀具上。所以,高速切削后如不及时将切屑排出,这些热量就会传递给工件和刀具。因此要对切削位置进行必要的冷却和并排屑,避免热量的传递和聚集。快速排屑还能避免了切屑的二次切削,有效保护刀刃,从而延长刀具寿命。
结语
高速切削加工技术是一种先进的、不断发展的综合技术,在机械制造行业特别是模具制造业中具有非常广泛的应用前景。用高速切削加工技术代替电火花加工,是加快汽车轮胎模具开发速度、缩短交货期、提高加工精度的主要途经。要充分发挥高速加工技术的优势,除必须具备高速加工机床外,还必须综合应用高速加工刀具技术、高速加工工艺技术、高速加工CAD/CAM技术以及冷却润滑技术。随着高速加工技术的不断发展,高速加工的优势和作用将越来越明显。
虽然高速切削加工技术在轮胎模具加工中已经突显出其独特的、明显的技术优势,但高速切削加工技术在我国轮胎模具行业中的应用时间还较短,到目前为止国内只有广东巨轮模具股份有限公司有较大规模地使用,其他的轮胎模具制造厂家即使有使用也是少数的、局部地的使用,所以对我国轮胎模具行业来说,高速切削加工技术的总体应用基础较差,缺乏成熟经验,整体技术水平不高,发展缓慢,特别是在高速机床和刀具的应用以及加工工艺方面还存在很多问题,需要产学研结合,加大投入,综合各方面力量大力推动高速切削在轮胎模具制造中的应用。
声明:本网站所收集的部分公开资料来源于互联网,转载的目的在于传递更多信息及用于网络分享,并不代表本站赞同其观点和对其真实性负责,也不构成任何其他建议。本站部分作品是由网友自主投稿和发布、编辑整理上传,对此类作品本站仅提供交流平台,不为其版权负责。如果您发现网站上所用视频、图片、文字如涉及作品版权问题,请第一时间告知,我们将根据您提供的证明材料确认版权并按国家标准支付稿酬或立即删除内容,以保证您的权益!联系电话:010-58612588 或 Email:editor@mmsonline.com.cn。
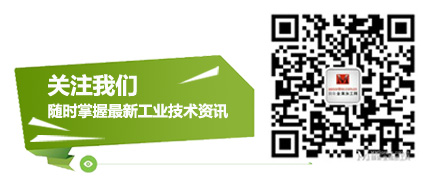
- 暂无反馈