汽车发动机加工:向刀具要效益
全球的汽车制造商们都在力争生产更经济和更节能的汽车,他们也拥有很多削减成本的方式,以实现这一目标。针对乘坐室,可选用新型材料;针对底盘,可以制造通用型、模块化的“平台”以及更多的标准零件;对于附件和电子器件,可以研发更加精密的组件。据统计,汽车工业投资的2/3用于购买汽车制造的装备。其中,刀具是最直接与被加工零件“亲密接触”的工具,它对最终产品的质量和制造成本有着非常直接的影响。以轿车生产为例,刀具的消耗只占其制造成本的3%,但是却影响到整个制造成本的25%甚至更多。
对于今年5,000万辆的乘用车制造计划来说,如果每个部件能节省一分钱,那么整个汽车行业将能削减8位数的成本。严苛的经济性要求、安全性要求,对于汽车配件供应商来讲,迫切需要新的更先进的加工工具,在成本、利润、效率、安全、节能等诸多纷繁复杂的因素所缠绕的“蜘蛛网”中,闯出“效益”一条路。
发动机加工:降低成本的关键所在
据美国底特律的IRN,
Inc.公司介绍,发动机的生产费用占到乘用车总生产成本的17%,然而却并不适用任何以上的成本削减方式。而汽油发动机生产,相比之下,是汽车生产环节中工艺最复杂、要求最严谨、所耗成本最高的部件。发动机一般为企业自主生产件,在设计方面的改进存在一定的局限性。在实际使用中高温、高压的环境,也决定了发动机只能选择金属材料。而即便使用最先进的生产技术,由于发动机自身对公差的严格要求,无论如何都无法避免金属加工环节,这其中也包括对铸铁的加工。例如,加工圆柱孔,在实现高金属去除率的同时,必须保证尺寸公差带控制在0.01mm内,圆度和圆柱度(无论相对值还是绝对值)在精加工时,形位公差达到0.001mm。
基于上述原因,在发动机零部件复杂的制造工艺中,发动机缸孔的加工,成为打破高成本的瓶颈,而如何降低其加工费用也成为各制造商们努力的方向。大量尺寸不一的阶梯孔、复杂结构内表面和细小的深油孔,加工精度要求极高,这就对加工所有的刀具结构、主切削刃形状、刀具材料、涂层以及断屑、排屑性能提出了较高的特定要求。发动机缸孔加工过程通常包括三个步骤:粗加工、半精加工和精加工。打破这一加工瓶颈,对于缩减汽车生产成本的效果十分显著。缩短了一个孔的加工周期,就意味着剩余的3、5或7个孔的加工周期的缩减(孔的数量取决于发动机型号)。
运用先进刀具 提升效率降低成本
德国一家大型汽车发动机生产工厂,在对其发动机缸孔进行加工时,刀具的第一步应用,是加工GG25灰铸铁套筒,其将被压入铸铝发动机缸体。该工步需要将深度为138mm的孔从74.50mm扩宽到76.10mm。尽管该工步名为“镗缸孔”,加工过程却更接近于垂直方向的镗铣;刀具直径依据缸孔最终直径制作,沿Z轴进刀的方式确保了加工孔的高同轴度。在最初加工时,该工厂采用专用刀具完成粗加工及半精加工。粗加工及半精加工工序均由夹持带5刃的CBN刀片至固定刀槽的铣刀完成。加工周期长达16.6s;两工步的刀具在清除切屑的问题上也表现得不甚理想,而对切屑的再次切削,不利于精加工,而且会磨损切削刃。这家汽车制造商希望得到性价比更高的替代方案:在原有工艺基础上,寻求更可靠的加工方式,大幅缩短加工周期,并保证工件表面的质量。
针对这种情况,伊斯卡刀具公司为其提供的解决方案是在同一刀体上采用两种装夹方式,夹持带涂层硬质合金刀片,一种刀座形式用于粗加工,另一种刀座形式用于半精加工。四片粗加工刀片平行于刀具顶面夹持于固定刀槽中。三片半精加工刀片垂直夹持于可调节式刀座,分布于铣刀圆周。粗加工刀片组约扩孔径1.00mm;半精加工刀片组扩孔径0.6mm。冷却液经由内冷却喷孔直达刀片切削刃处,以确保有效排屑。为消减振颤,半精加工刀片组以非对称的方式分布于圆周。同时,立装刀片,刀片与节圆呈切向排列而非垂直于节圆呈放射状安装。其原理是令主切削力指向最厚实的刀片截面从而提高每刃承载能力。切削负载直指刀体,在有效减振的同时获取更长的刀具寿命。此外,刀片立装夹持,螺钉免于承受拉应力,可以确保切削加工更可靠。此外,伊斯卡通过分析客户的机床设置,更新切削参数,来探寻加工周期缩短的因素。伊斯卡并未更改机床的转速,仍为1,500rpm,切削速度 Vc=360 m/min,刀片每刃移除材料0.50 mm。而是将进给量从0.07 mm/齿提高到了0.10mm/齿,进而显著提升工作台进给及进给率。
伊斯卡TANG MILL面铣刀系列
在几个月的新工艺试用之后,这家汽车制造商发现,运用伊斯卡新研发的特制刀具,缸孔加工的周期比以前缩短了44%。带4个缸孔的发动机,在相同切削条件下,每一个缸孔的粗加工复合半精加工从原先到16.6s缩短到现在的9.2s。同时,加工过程中所采用的刀具数量也大大下降,帮助用户减少了刀片消耗。曾经需要各自刀具的工步,如今用一把刀具可以同时完成加工。意料之外的节省,除了因为涂层硬质合金刀片较CBN刀片更加经济;还由于刀片立装夹持,使每个刀片切削刃更多,共同有效延长了刀具寿命。作为发动机的另一重要部件,连杆与曲轴和活塞销配合的孔要求具有很高的精度,多采用粗镗、精镗、铰孔和抛光的加工工艺,其中铰孔精度和难度最高。某汽车零部件制造商在加工连杆大头孔时,使用了山高刀具的新型X-Fix大直径多齿铰刀。在使用过程中发现,这款铰刀的直径覆盖范围从40mm到155mm,能够获得IT6级公差,使用非常方便。而且这款铰刀的齿数比同类型刀具更多,包括了3、5、7、9四种齿数,大大提高了加工效率;而且刀具加工过程中非常稳定可靠,极大地降低了加工成本。客户对此非常满意。山高刀具(上海)有限公司技术总监王玮不久前在2011上海大学先进制造工艺与刀具技术研讨会上向与会的专家学者介绍了山高这款X-Fix新型铰刀在汽车行业的一些成功的应用案例。
山高刀具的XFix大直径多齿铰刀
据介绍,这款铰刀成功地实现了最高的进给量、最高的性能和最高的精度三者的结合。其采用模块化结构的刀杆,带Capto和Graflex系统的宽范围的接长杆系列,可以实现高达6.5X D的铰削深度,铰刀的倒锥由精密制造的刀片座提供,因此无需进行调整。X-Fix铰刀具有8个切削刃的可转为刀片,每片刀片覆盖直径范围从40mm到155mm;用于高进给性能的多齿,实现高产量加工。要设置直径,仅靠一个螺钉即可固定刀片,而唯一要记住的设置值是25μm。获得专利的预载导向条系统可以保证切削过程的稳定性,并确保可靠的刀具寿命。加工操作的质量和安全性得以保证,并且简化了刀具成本管理。为了降低库存,用户可以对所有Xfix(从直径 31.5 到 60.5 mm)都使用相同的刀片并且无需重磨。稳定的刀具寿命、最新的镀层技术以及刀片每刃的低成本都大大降低了 XfixTM铰削加工的成本。
声明:本网站所收集的部分公开资料来源于互联网,转载的目的在于传递更多信息及用于网络分享,并不代表本站赞同其观点和对其真实性负责,也不构成任何其他建议。本站部分作品是由网友自主投稿和发布、编辑整理上传,对此类作品本站仅提供交流平台,不为其版权负责。如果您发现网站上所用视频、图片、文字如涉及作品版权问题,请第一时间告知,我们将根据您提供的证明材料确认版权并按国家标准支付稿酬或立即删除内容,以保证您的权益!联系电话:010-58612588 或 Email:editor@mmsonline.com.cn。
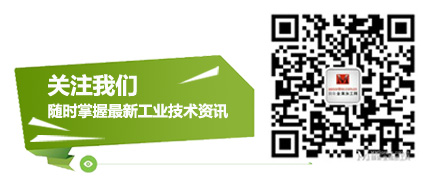
- 暂无反馈