船舶业:我国由大到强怎么走
2010年,我国造船完工6560万载重吨,新接订单7523万载重吨,手持订单19590万载重吨,分别占世界市场的43%、54%、41%,均居世界第一。这意味着我国船舶工业在总量上已经超越韩国和日本,跃居世界第一。
这个意料中、迟早会诞生的“世界第一”并没有引起人们太大的兴奋。因为,一个尴尬的现实仍然摆在面前:尽管在总量和规模上已经是世界第一,但在科技水平和核心竞争力等方面,我国船舶业与发达国家还有不少差距,还不是造船强国。
今后5年,是我国船舶工业加快转型升级、实现由大变强的关键时期。船舶工业由大到强之路怎么走?突破口在哪里?
1.由大到强,这一步有多远?
“造船大国到造船强国,看上去一字之差,却有很长的一段路要走。”中船重工集团党组成员孙波说。
在船舶业三大指标中,最能显示未来走势的是新接订单量。我国去年新接订单占世界市场54%,超过一半,的确很“大”。
但仔细分析这54%的构成,就会发现还谈不上“强”。
2010年,随着国际金融危机影响减弱,国际航运市场反弹,散货航运效益提升,国际市场散货船需求量上升,新订单以散货船为主。技术含量和附加值相对低些的散货船恰是我国船舶企业的强项,因此我国企业新接订单占了优势。
过去几年的那轮“造船热”中,由于散货船是市场需求最大的船型,使得我国不少造船企业沉浸于眼前的繁荣,忽视了高技术船舶的研发。
相反,日韩等造船强国即便在金融危机期间,仍在坚持高端船舶品种的开发,并牢牢把握住了高技术船舶的市场订单。
此外,劳动生产率低、配套能力差、业务领域比较单一等问题,也是制约我国成为造船强国的关键因素。
这种大而不强的局面,对船舶业的可持续发展十分不利。
据船舶工业协会有关专家介绍,今年以来全球船舶市场需求出现较大变化。从船型看,集装箱船成交量持续上升,其中大型、超大型集装箱船的订造量增长更为迅猛;特种船、海洋工程装备的订造量大幅攀升。全球新船订单的争夺已经呈现出技术、品牌和质量的竞争。
此外,散货船运力严重过剩和航运市场持续低迷的双重打击,使散货船运费暴跌,多数船东出现亏损,导致散货船交付更加困难。
“未来,低附加值的船舶品种会不断受到市场变化的冲击,风险将进一步加大。而高附加值的船舶,需求会不断上升,价格稳定。”上述专家认为,改变目前过于依赖散货船订单“一支独大”的局面,全面推动船舶工业由大到强,已经迫在眉睫。
2.优化提升主流船型,进军“三高”船型
4月底,由沪东中华造船有限公司建造的首艘8888箱超大型集装箱船在上海正式命名。这艘被命名为“东方北京”的新船总长334米,超过了3个国际标准足球场的长度。首次采用了新型柴油电喷主机,进一步提高了船舶的自动化程度,并能在航行中大量节省能耗。这是迄今为止我国造船企业自行设计和建造、拥有完全自主知识产权的最大型集装箱船。
“我国要向造船强国目标奋进,不仅要‘振兴’更要‘调整’。”中国船舶工业协会副会长于世春指出,高技术、高附加值、节能环保型船舶已经逐渐成为船东首选,这正是我国调整的方向。
近年来,面对国际船市的大幅波动,我国两大船舶企业——中国船舶重工集团公司(简称“中船重工”)和中国船舶工业集团公司(简称“中船集团”)仍然取得较好的经营业绩,造船完工量位居世界前列,新接订单逆势提升,与企业加大科技投入、不断开发新船型密不可分。
有关统计数据显示,中船重工近年累计承接18万吨好望角型散货船69艘, 30万吨超大型油船69艘。中船集团则向市场推出了7.6万—32万吨系列原油船,1400—8530箱集装箱船等一批具有自主知识产权的优良船型。同时,两大集团都已经具备了1.35万箱超大型集装箱船的设计建造能力,达到世界先进水平。
产品结构优化,一方面是散货船、油船、集装箱船这三大主流船型的优化提升,另一方面则是进军高端。“十二五”规划提出,要重点发展大型液化天然气(LNG)船、大型液化石油气(LPG)船、远洋渔船、豪华游船等船舶。
以被誉为船舶业“皇冠上的明珠”的LNG船为例,因为能够把天然气在零下162摄氏度进行液化运输,LNG船不同于一般油船和集装箱船,是国际公认的高技术、高难度、高附加值“三高”船舶。过去10多年里,韩国等少数国家一直垄断LNG船的市场,而中国作为新生力量,正在努力进入这一领域。
“十一五”期间,中船集团突破了LNG船建造关键技术,成功交付了5艘14.7万立方米LNG船,实现了中国LNG船建造零的突破。大连船舶重工集团也已完成22万立方米和26万立方米LNG船的设计研发,具备推向市场的条件。
我们在不断向高端进军,日韩企业并没有停下脚步,其高端船舶的技术优势仍然明显。孙波认为,发展高技术、高附加值船型,不仅要进一步加大研发投入,也要求船舶企业全面转变管理方式,发展与之匹配的现代造船模式。中船重工在“十二五”期间将不再搞大的产能投入,而要着力提升“软管理”,提高生产效率和精细化管理能力,把产能充分发挥出来,以“精”取胜。
3.吃透国际新标准,提高核心竞争力
近日,由中国重工青岛双瑞海洋环境工程有限公司研制的船舶压载水处理系统通过了国际海事组织专家组的评估和中国船级社的认可,成为我国与国际同步、唯一获得双项认证的该类产品,并实现接单。
船舶航行过程中,为了调节平衡和吃水深度,都需要在船舱内导入压载水。压载水排放过程中携带的有害水生物会破坏接受水域的生态平衡。为了控制这一问题,国际海事组织通过了《国际船舶压载水和沉积物控制和管理公约》,要求各类远洋船舶不得晚于2017年安装压载水处理系统,使压载水达到排放标准。
一旦公约生效,若我国没有自主知识产权的相关技术和产品,必然要受国外技术和产品的制约。而青岛双瑞研发成功的压载水处理系统,意味着我国能够凭借完全自主知识产权的技术与国外在同一起跑线开展竞争。
近年来,在追求更安全、更环保趋势的推动下,国际海事组织不断推出新规范和新标准。“十二五”期间,包括新船能效设计指数、压载水公约、船舶噪音控制等在内的重要国际新规范、新标准将对船舶工业带来新考验。
新规范新标准将是一把双刃剑。适应了,就能提高核心竞争力,与其他造船强国一较高下。不适应,就会面临巨大的成本压力和更高的技术门槛。
“十二五”规划纲要提出,我国船舶行业要适应国际造船新标准,建立先进造船模式。只要参与国际市场竞争,就无法绕开新标准。吃透国际标准、提高核心竞争力是我国船舶工业真正做强的必由之路。
客观上讲,这些国际新规范、新标准对我国大部分船企而言,要求还比较苛刻。专家表示,要完全满足日益严格的新规范、新标准要求,企业不仅要从技术层面进一步优化船体线型、降低空船重量、大量采用环保动力系统等,还要从操作层面进一步改善作业环境,加大对员工的培训力度。
“在适应国际新规范、新标准的同时,我们还应该进一步提高国内标准水平。”孙波表示,船舶企业也应结合实际主动提出意见和建议,为增强我国在标准制定领域的国际话语权做出贡献。
4.发展海洋工程装备,关键要提高利润水平
日前,从巴西海域传来消息:由大连船舶重工建造的国内首座技术性能最先进的3000米深水半潜式钻井平台正式投入油井钻探作业,这座“海上巨无霸”最大作业深度达10000英尺,可满足在世界各海域作业要求。经过实践检验,其技术性能完全达到设计标准,这是我国在高精尖海洋工程产品建造上取得的又一重大突破。
放眼整个海洋,除了传统的造船,船舶企业还有十分广阔的空间。其中,海洋工程装备既是与造船最接近的领域,也是高技术、高附加值的产品。
“十二五”规划纲要明确提出推进海洋经济发展,培育壮大海洋工程装备制造等新兴制造业。同时提出,船舶行业要加快海洋移动钻井平台等自主设计建造步伐。
中船重工“十二五”将力争进入世界500强。“500强看的不是产量规模,而是看销售额。”孙波介绍,建造一台30万吨油轮,售价约为1亿美元;而生产一座半潜式钻井平台,尽管核算载重吨仅为4万吨,售价却可以达到约6.5亿美元。“要进入世界500强,要建设造船强国,发展海洋工程装备必不可少。”
目前,中船重工已经成功建造了高技术含量的JU2000型、CJ46型等10余座自升式钻井平台,掌握了深水半潜式钻井平台关键技术。中船集团近年来则成功交付了国内吨位最大、技术最先进的30万吨海上浮式生产储油船(FPSO),使我国在FPSO的开发设计方面处于世界先进水平。应该说,我国在海洋工程装备的设计制造能力上,与造船强国相比有一定的竞争力,这也将成为借助海洋工程装备打造造船强国的重要基础。
前景美好,但从振华重工等上市公司公布的2010年年报来看,海洋工程装备业务毛利率不足10%,与国际平均30%的水平相比明显偏低。专家表示,在不断提高设计制造能力的同时,我国企业还要努力提高劳动生产率,降低成本,提高产品的利润水平。
声明:本网站所收集的部分公开资料来源于互联网,转载的目的在于传递更多信息及用于网络分享,并不代表本站赞同其观点和对其真实性负责,也不构成任何其他建议。本站部分作品是由网友自主投稿和发布、编辑整理上传,对此类作品本站仅提供交流平台,不为其版权负责。如果您发现网站上所用视频、图片、文字如涉及作品版权问题,请第一时间告知,我们将根据您提供的证明材料确认版权并按国家标准支付稿酬或立即删除内容,以保证您的权益!联系电话:010-58612588 或 Email:editor@mmsonline.com.cn。
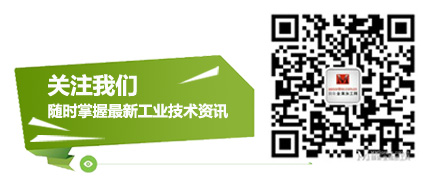
- 暂无反馈