瓦尔特应用案例:以铣代磨 以铣代挤中的技术攻关
高速加工,尤其对具有大去除量金属加工特点的航空制造业而言,是实现高效率制造的核心手段。起源于德国学者Carl.Salomon博士的假设:“线速度超过一定值后,随着线速度的增加,切削温度不升反降。”经过多年的实践,该假设得到证实。特别是在1992年,德国Darmstadt工业大学的H. Schulz教授详细阐述了高速切削加工的概念及其涵盖的范围,他认为对于不同的切削对象,如下图所示的过渡区即为通常所谓的高速切削范围,那是当时金属切削工艺技术人员所期待实现的切削速度。如今,高速切削作为面向21世纪的一项高新技术,因其具有高效率、高精度和高表面质量的基本特征,越来越多的实践应用证明了其能产生巨大的技术经济效益。
针对某型号产品,在铣削高硬材料和铣削高精度转子柱塞孔的生产过程中,我们通过高速铣削的方法,应用德国瓦尔特(瓦尔特官方网站,瓦尔特社区,瓦尔特产品一览,瓦尔特应用案例)的标准与非标刀具,以铣代磨、以铣代挤,最终实现了设定的目标,完成了技术攻关,有效提升了整体制造水平。
在实际加工中,我们主要有两个应用方向:第一,利用高速切削加工超硬材料。传统及国内同行普遍采用磨削加工,不仅效率低、单件工时较高,而且使用磨头消耗大,刀具成本高。尽管近年来随着CBN、金属陶瓷、陶瓷等刀具的应用,渐渐开始使用新的切削方式加工超硬材料,但是普遍存在切削区域局部温度高,有精加工面表层金相组织变质的现象。高速加工会降低切削区域温度,引起我们的兴趣。第二,是在加工有色金属(尤其是铝合金)时的应用,为降低在薄壁、细深腔等对切削力较为敏感的零件的切削变形,切削深度要经量选低,但切削深度低,在传统的机床上,零件的加工效率自然降低,高速加工转速高、进给快,可以有效弥补切削深度变小的效率损失。
以铣代挤
以生产某柱塞泵产品为例,其中关键配合孔材质为铸铜、尺寸为φ10,公差要求为0.005,圆柱度要求0.003,粗糙度要求0.2,孔长径比为6。为保证该孔的尺寸及技术条件要求,原工艺方法为镗、挤加工,即先镗加工预留合适的挤光余量由挤光刀加工。尽管效率较高,但存在最大的问题是:铸铜材料有缺陷,往往在挤光的过程中不可控,合格率不高。并且挤光工序为最后工序,工序报废后经济损失较大。
在引入高速铣机床后,以及深入了解了高速铣削理论后,我们决定使用高速铣的方法来进行技术攻关。我们的工艺实践策略为粗、精加工严格分离;分层铣削;定期检测更换精加工刀具。
粗、精加工分离。主要是刀具的分离,粗加工以快速去除余量为主,主要采用螺旋插铣的铣削方法,对刀具要求不高。精加工加工策略与初加工完全不同,对刀具对跳动及刀尖尺寸要求高。对刀具的要求首先体现在几何尺寸上,首先要求刀具夹持后的跳动不大于0.004,这项指标体现的是工具供应商在刀柄和刀具制造上的综合实力,在瓦尔特工程师的指导下,我们通过反复夹持试棒测量,得出:瓦尔特热涨刀柄的反复定位精度不大于0.002,夹持瓦尔特铣刀后,刀尖跳动不大于0.004,远远高于0.008到0.012的平均水平,满足了刀尖跳动要求。另外,瓦尔特工程师根据我们零件的工况,在刀具几何角度上选取了大前角、大螺旋角的刀具、在材料上选择了耐高温的刀具材料,以及硬度高、摩擦系数小的涂层材料,有效减小了加工阻力,避免在加工过程中出现振动问题。实践证明,刀具加工过程中,不仅接触角度大,多刀齿同步工作,切削进刀退刀平稳,还进一步减少了振动,更耐磨,刀具寿命也更长。
分层铣削。主要是在精加工的过程中,我们对现有常用的铣削方式进行了一定的试验和摸索,发现:螺旋下刀铣无法满足零件圆柱度和光度要求,圆柱度最好在0.015,光度不超过0.4;侧铣无法满足零件的圆柱度要求,加工后孔上大下小有0.008-0.01的锥度,分层铣的方法能够同时改善圆柱度和光度水平,但分层铣削的分层深度直接影响着零件的加工效率,经试验在经济性和质量的平衡下,分层厚度为0.4。这是铣削的关键参数。
定期检测并更换精加工刀具。精加工刀具直接影响质量,如此精度的尺寸,刀具磨损超限的结果就是产品超差。使用目视刀具涂层磨损情况,与使用高倍的对刀仪检测,能有效检测刀具磨损情况。在涂层脱落或刀尖跳动超出0.006的情况下及时更换刀具,有效的保证了产品的稳定性。除此之外,刀具磨损后经国内专业的刀具厂商返修,也节约了大量的刀具成本。
按每批产品50件投产来计算,提升效果如下:
以铣代磨
生产中,有相当大一部分产品需要在热处理后进行加工,尤其是高硬度材料(HRC55以上)。对回转类零件,一般采用内、外圆磨床加工,非回转类零件一般采用坐标磨床,效率极低,经济性也不好。
我们应用高速铣削解决了这些问题,不仅实现了高效、低切削力,在某些场合完全取代坐标磨床的作用。主要应用特点如下:
加工余量对以铣代磨加工的效率影响非常大。一般侧铣加工余量不大于0.02,否则刀具急剧磨损。
线速度严格按刀具样本制定值调整。因为新的加工理念使生产环节的积累不足,而刀具使用指南是厂商技术积累的成果,要有“拿来主义”。以往,我们在加工高硬材料方面可谓空白,偶尔加工HRC48-52材料过程中,总会出现加工效率低、刀具热磨损速度快、刀具出现崩刃现象、产品加工后还有啃刀现象、加工精度不稳定等问题。在与瓦尔特工程师多次交流后,我们从源头(刀具选型:我们选取瓦尔特超硬加工系列材料,采用小前角、小螺旋角、不等齿距、不等螺旋角的刀具几何尺寸系列,能有效的增加刀具韧性,耐热性高),过程(参数应用,主要是采用低切削量、高转速、高进给的参数组合,一般将切削深度不大于0.04,转速提升至75m/min,进给在40M/min)优化了加工顺序及采用螺旋进、退刀方式,以及刀具翻新(刀具一旦磨损镀层磨损至刀具发白或磨损量超过0.012,进行返修),这样一个完整的刀具应用管理周期进行了全面的调整。可以说,完整解决方案的应用,有效保证了目标的最终达成。
刀具一定有针对性,一般加工高硬材料的刀具材料均为特殊开发,严格控制刀具材料中粒度不大于0.02的粒子不低于80%,钴含量不高于3%,加入钛、铌、钼、铝的等元素,采取合理的热处理工艺手段,选取硬度高(HV>3500)摩擦系数小于0.25的涂层,采用物理气相沉积的涂层方法,使刀具材料的综合性能得到保证。
关于中航工业金城南京机电液压工程研究中心
中航工业金城南京机电液压工程研究中心是我国航空机载机电系统的研发中心和生产基地。具有完整的预先研究、型号研制、设计制造、试验交付和维修服务的手段和能力。现有职工3000 余人,公司先后为60 多个机型37 大机电系统提供产品和配套附件。目前拥有的空中加油装备、恒速传动装置、应急动力装置、空气涡轮起动机、燃气涡轮起动机、高压除水环境控制系统、三轮涡轮冷却器、高性能电液伺服阀、燃油泵、飞机地面操纵系统等核心技术和产品,在国内具有不可替代性。同时,民航机电产品维修居于国内领先地位。
图2. 薄维斌,中航工业金城南京机 电液压工程研究中心工艺工程部
图3. 在引入高速铣机床后,以及深 入了解了高速铣削理论后,我们决定使用高速铣的方法来进行技术攻关。我们的工艺实践策略为粗、精加工严格分离;分层铣削;定期检测更换精加工刀具。
图4. 在铣削高硬材料和铣削高精度 转子柱塞孔的生产过程中,我们通过高速铣削的方法,应用德国瓦尔特的标准与非标刀具,以铣代磨、以铣代挤,最终实现了设定的目标。
(薄维斌 中航工业金城南京机电液压工程研究中心工艺工程部)
声明:本网站所收集的部分公开资料来源于互联网,转载的目的在于传递更多信息及用于网络分享,并不代表本站赞同其观点和对其真实性负责,也不构成任何其他建议。本站部分作品是由网友自主投稿和发布、编辑整理上传,对此类作品本站仅提供交流平台,不为其版权负责。如果您发现网站上所用视频、图片、文字如涉及作品版权问题,请第一时间告知,我们将根据您提供的证明材料确认版权并按国家标准支付稿酬或立即删除内容,以保证您的权益!联系电话:010-58612588 或 Email:editor@mmsonline.com.cn。
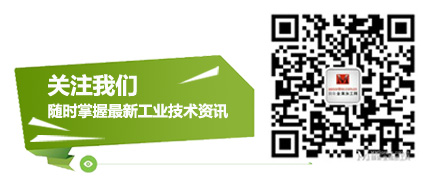
- 暂无反馈