小品类刀具加大创新带动全行业实现突围
【编者按】目前,我国进口刀具基本上占据了加工行业的高端用户,国产刀具本应在为这些制造领域提供刀具服务中具有天时、地利、人和的优势。但实际上。特别是汽车发动机制造车间、飞机发动机制造企业机加工车间或汽轮机制造车间,高效、高精度的机加工刀具中几乎被进口刀具垄断,很难看到国产刀具的踪影。而国产刀具大多应用在中、低要求的客户群里,如农业机械、摩托车、农用车、通用机械及中低档的机械制造工业。
据悉,制造业粗放式发展导致机床和刀具的发展极不平衡,国外发达国家数控机床和刀具的消费比为2:1,而国内的比例却很低,刀具消费总额还不到机床消费总额的1/5,很多制造企业花大价钱购买机床,却在刀具消费上缩手缩脚,不愿意购买先进高效刀具,但是,传统刀具的市场需求长期居高不下,这也是国内很多刀具企业不愿进入先进高效刀具生产的重要原因。
应该让用户需求和刀具企业成为创新主导,龙头企业应在技术应用领域做好带头示范作用。不过,国内部分重点骨干企业和新型优秀民营企业在发展现代高效刀具方面跨出了非常可喜的一步,如株洲钻石、厦门金鹭以及阿诺刀具等,这些企业重视技术进步,将服务放在首位,相关领域取得了明显成效。同时,“十二五”期间,国产高效刀具的高端市场占有率,可能从目前的15%左右提高到30%~40%,在航空航天、能源交通、国防军工等现代制造业,都将拥有几个顶级生产线,我国刀具企业的竞争力将会从整体上大幅提升。
同时,这也对我国的传统刀具行业提出了更大的挑战。在我们平时所接触的众多民营刀具企业中,产品大都是“多而全”,缺乏分类和针对性。而就航空航天、轨道交通和海洋装备这三大与切削工具联系最紧密的高端装备制造行业而言,国内几乎没有专门针对三个领域中任何一个领域的专家,这说明了我们跟发达国家的差距不是一丁点儿。
没有专家,说明了我们缺乏专业细分化的产品。与此同时,我国刀具企业普遍存在的问题是自主创新能力弱,市场上的重复投资已经呈现常态化,企业之间往往通过价格竞争来赢得客户而非独特产品。
这种情况下,高端刀具领域对中国企业来说似乎都可望而不可及。而要突破这层屏障,行业应该加强细分,因为小品类更容易实现各个突围,避免全品类的一哄而上。
声明:本网站所收集的部分公开资料来源于互联网,转载的目的在于传递更多信息及用于网络分享,并不代表本站赞同其观点和对其真实性负责,也不构成任何其他建议。本站部分作品是由网友自主投稿和发布、编辑整理上传,对此类作品本站仅提供交流平台,不为其版权负责。如果您发现网站上所用视频、图片、文字如涉及作品版权问题,请第一时间告知,我们将根据您提供的证明材料确认版权并按国家标准支付稿酬或立即删除内容,以保证您的权益!联系电话:010-58612588 或 Email:editor@mmsonline.com.cn。
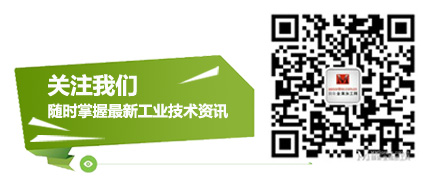
- 暂无反馈