测量臂在检测复杂自由曲面中的应用
测量臂也叫关节臂,也有人称便携式三坐标测量机,该系统是一种新型的多自由度的非笛卡儿式坐标测量系统。它将6 个转动臂(在每个关节中都安装有角度编码器)和1 个测头通过6 个旋转关节串联,关节与关节之间由长度不同的杆件连接而成,6 个角度编码器给出了各个关节的相对转动量,从而决定了测头的位置。测量臂的一端固定于基座上,测量头可以在空间自由转动,这样就形成了一个空间开链连杆机构,构成了一个半球形的测量空间。测量人员可以手工移动测头进行测量。利用计算机上携带软件计算出被测点的位置,通过数据处理得到待测参数值或偏差。
用我公司的ROMER 测量臂检测某飞机工装的定位型块。ROMER2160 的技术参数:
测量范围:以基座为圆心,1800mm 为半径的球;重复测量球体的精度+0.049mm ;重复测量锥体的精度+0.054mm ;测量长度精度+0.074mm ;工作温度+10 ℃ ~+40℃ ;湿度:5% ~ 90% 非冷凝;功率补偿:100 ~ 240VAC( ±%10) ,50/60Hz A(±3Hz);配备接触式测头。
复杂曲面的测量
1 测头校准
测量工件前, 首先要进行测头校准, 以消除由于环境条件变化所产生的探针半径误差对测量结果的影响, 下面简单介绍ROMER2160 校准方法。
(1)开机并进入GDS。
(2)选择Probe Calibration。
(3)在Select type of probe 下拉菜单中选择Contact probe。
(4) 在New probe to calibrateindex 提示框中输入序号。
(5)Enter probe diameter 项中,输入“6”(因为需要校准的为6mm测头)。
(6) 屏幕出现Machine filealready exist. Do you want to replace it
(7)进入校准过程。点击Runall。
(8)Install probe 1(15 diameter)。安装1 号15mm 金属测头。点击OK。
(9)(此项也可在预备工作时候做)在一个标准平面(平面度要好)上,点三点做为等边三角形的3 个顶点。三边长度均为50mm。
(10)使测头垂直于标准平面。按照1、2、3 顺序测量3 点。每点一点,须按确认按钮。之后,屏幕出现Contact probe 后,更换6mm 直径测头,点击OK。
(11)使测头垂直于标准平面。按照1、2、3 顺序测量3 点。每点一点,须按确认按钮。
(12)倾斜测头,使测头与平面夹角45°、135°。按照1,2,3 顺序测量3 点。每点一点,须按确认按钮。
(13)倾斜测头,旋转E 轴90°,使测头与平面夹角45°、135°。按照1,2,3 顺序测量3 点。每点一点,须按确认按钮。
(14)屏幕出现Measurementcomplete, start calculation. 点击OK,开始计算。
(15)E nt e r pro be c o mme nt i fnecessary. 可输入“6(050914)”:意思为2005 年9 月14 日,6mm 测头。
(16)结束过程。然后选择最新校准6mm 测头、测量块。如结果不好,重新此过程。
2 零件分析
根据工件的设计基准或工艺基准, 找正工件坐标系。而对工件的装夹和调整几乎没有要求, 只要在测量过程中工件能保持稳定即可。
以某飞机工装的定位型块作如下分析:该零件的复杂型面进行数控加工,但由于加工过程中的误差较大,使得2 个基准孔(TH1,TH2)的位置与数模不相符,即已没有两个基准孔理论值,所以用这个基准孔无法检测型面。
3 确定方案
在这种情况下,用ROMER 测量臂迭代拟合功能来解决这类技术难题。首先分析被测物体的大小,然后采取牢靠的装卡方式,将零件装卡在平台上,与设备保持相对位置关系不变;分析被测零件的曲率变化,选择6mm 的红宝石测头,避免零件的曲率过大而造成测量误差。
4 开始测量
(1)在数模上取点。
首先在powerinsper 软件中以CATPAT 或IGS 格式导入该零件的三维数模,分析被测零件的型面特征点,并在三维数模上手动取出对应的点,数量不小于6 个,而且这6 个点要在6 个法向面上,然后在被测零件的相应位置进行实测点。要注意的是,这几个点的采集顺序要和在数模上取点的顺序一致。通过测量指定点,借以检测曲面的加工精度。在这个过程中的操作顺序是:首先在数摸上用动态点编辑器采集一些点,尽可能取X ,Y ,Z 三个方向;然后新建检测组,测量已经选择的曲面点。
声明:本网站所收集的部分公开资料来源于互联网,转载的目的在于传递更多信息及用于网络分享,并不代表本站赞同其观点和对其真实性负责,也不构成任何其他建议。本站部分作品是由网友自主投稿和发布、编辑整理上传,对此类作品本站仅提供交流平台,不为其版权负责。如果您发现网站上所用视频、图片、文字如涉及作品版权问题,请第一时间告知,我们将根据您提供的证明材料确认版权并按国家标准支付稿酬或立即删除内容,以保证您的权益!联系电话:010-58612588 或 Email:editor@mmsonline.com.cn。
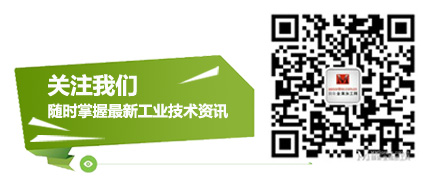
- 暂无反馈