粗解车架结构
1、传统式一体化车架
传统意义上的一体化车架,就是将主车架、承载梁、外壳等等看作一个整体,各部分通过焊接将之接合。将两种没有分支结构的车架形式介绍完后,剩余的两种形式都有众多的分支结构。首先是一体化车架设计,英文称作Monocoque。如果从字面上解释一体化设计会较为复杂,但站在车厂的角度上,一体化设计的出现,可以令车辆的生产速度获得前所未有的提高,虽然对于生产车架各部分所需要的加工机器的成本巨大,但是生产效率的提高、自动化设备的广泛应用,令单件部件的制作成本降低,所以某些车厂可以年产百万辆,如果换了其他机构,是根本不可能实现的。
RX-8的车架设计,属于较为传统的一体化布局。
FORD的Mustand也是传统式一体化布局,可以看到,承载梁、叶子
板等等,都是车架的其中一部分,通过焊接将各个构件接合在一起。
虽然目前几乎所有的量产车型都采用一体化车架设计,但其也有诸多缺点,例如重量和金属材料的消耗量都是不可避免的,但因为其拥有不错的抗撞击能力、有效使用空间大等诸多有点,此设计还是被保留下来,目前更多的汽车厂家在不遗余力地探索基于此次设计下的有效解决办法,从而也引申出多种一体化形式。
Jaguar的全铝合金一体化车架,一改过去全部使用钢板的时代,铝合金能
有效解决了锈蚀、重量等问题,但要提高刚性,则需要更高明的力学设计。
2、轻量化高刚性一体化车架(ULSAB Monocoque)
首先需要说明,该车架形式属于一体化车架的一个分支,而且属于少数族类,其整个生产过程与传统的一体化车架一样,只是在各部分构件上的制作上有所不同,大家都知道轮圈的分类中,有铸造轮圈和锻造轮圈,而锻造也分为低压锻造和高压锻造两种,高压锻造刚性高,而低压锻造则在刚性和韧性之间找平衡点。轻量化高刚性一体化车架其实与普通一体化车架的区别就如同此种区别。轻量化高刚性一体化车架的生产过程中,所有车架内的部件都是依靠高压成型的,而普通的一体化车架则多为冲压成型,两者的区别就在于成品内部的分子排列上,高压成型的分子结构细密、均匀,而冲压成型则会出现并不均匀的应力分布,令焊接后整车刚性不足的缺点。
从E46时代开始,BMW的三系便开始使用这种名为轻量化高刚性一体化车架设计,因为材料加工工艺提高,令原来某些细节上的补强可以被取消,从而达到更佳的整体刚性和轻量化诉求。
ULSAB的概念是有保时捷提出,并使用,而时至今天,这种比相同设计下的一体化车架要轻一半,刚性提高一半的设计,只有被少数车型的几个车型所使用,成本相对较高是其没有被广泛使用的其中一个重要原因。
3、碳纤维一体式车架
看到碳纤维一词,中国汽车技术网的读者相信都心里有数了,能用上这些车架结构的绝非普通车型。不错,这种结构绝对上少数民族中的贵族。碳纤维一体化车架最早出现在赛车上,当然也是那项每年烧掉数十亿美元的一级方程式赛车,而在街车上,最早的,真正能被称为碳纤维一体化车架的车型是1993年发售的Mclaren F1,该车的风头被其宝马的627匹V12引擎和破纪录的360公里极速所抢去,从车架设计角度上看,这台车同样是世界之最,最早使用全碳纤维一体化设计的车架,从下面这张仅能找到的图片上,就可知道F1是何等的奢华,无论引擎、悬挂还是三名成员都被包裹在那个碳纤维车壳里,无论整体刚性还是重量,普通的汽车均难望其背。麦拿伦F1之后,便是1995年的法拉利F50和ENZO,两者的设计均来自一级方程式,当然也就名正言顺地用上这种碳纤维一体化设计,不过与之前的麦拿伦F1不同,F50和ENZO更贴近一级方程式,碳纤维部分只有乘客座舱及前方的悬挂支撑梁,后方则由引擎和变速箱完全充当作车架的后部结构。想想这三台车在车坛的地位,不是贵族吗?
上图为麦拿伦F1的全碳纤维一体化车架;下图则是法拉利F50的。
F50的俯视图,尾部只有引擎和变速箱充当车架的后部结构一体化概念只实现在成员舱和车头。
后悬挂系统及引擎周边全部安放在引擎和变速箱上。
碳纤维一体化车架的设计在许多介绍中并不止这区区的三台车(民用街车),有的连同959、288GT0甚至F40等也划归此项,不过笔者不敢苟同,既然作为一个独立的设计形式,80年代的那些只是某部分实现了碳纤维化,相比之下没有上述的三台来得彻底和统一。所以介绍“碳纤维一体化车架”还是只有三个主角。
1987年的F40,只是在乘客座舱等部分实现了碳纤维化,而其他机件仍
构筑在空间管阵车架上,所以不能将之划入“碳纤维一体化车架”范畴。
4、盆式铝合金一体化车架
这种车架只有一个车厂在设计制作,那就是Lotus莲花车厂,当然也包括了购买其车架成品的OPEL。此款车架最先被应用在Lotus的Elise上,同时也让Elise成为了经典,一台最具操控性能、最具赛车化特性的街道超级跑车,之所以能被划入超跑序列,最大的原因并不是其只有百来匹的输出,而是其优异的车架设计。盆式铝合金是一个全新的概念,其所有部分均采用铝合金制作,然后各部分通过胶水(环氧树脂)粘合在一起,成为一个整体,从而诞生了盆式铝合金一体化车架的概念。
这就是莲花车厂委托丹麦铝窗公司制作的盆式铝合金一体化车架,整个车
架的重量只有65公斤,但抗扭性能超人,也是Elise受欢迎的主要原因之一。
数量不多的铆钉加上特殊的环氧树脂胶水,成为了整个车架
的连接方式。不过其通过撞击试验,证明胶水同样很安全。
空间管阵式车架
1、传统空间管阵式车架
空间管阵式车架是目前众多规模化生产的车架形式里,整体刚性最好的一种。传统意义上的空间管阵式车架设计,概念同样来自碳纤维一体化之前的一级方程式赛车,在碳纤维仍未被发现前,大部分的方程式赛车都会使用这种结构。之后随着房车赛事和一些超级跑车的赛事开始兴起,这种只在高处不胜寒的车架结构慢慢被人们认识。不过,其结构导致了其虽然属于批量生产的结构,但相比一体化车架可以大批量机械化生产,空间管阵式仍只能进行劳动密集型加工,例如法拉利已经算是产量最高的超级跑车厂和空间管阵式的忠实拥护者,但是在铝合金管阵车架被应用前,其年产量也就三千台上下,后来由美国铝材加工铝合金空间管阵车架后,产量才得以提高,不过年产量还是不超过5000辆,同样使用该设计的其他超级跑车厂,其产量则更少。
最为典型的空间管阵式车架结构,其采用的管材多为高拉力钢管,
也就是铬钼钢管。而结构形式则千变万化,没有特定的要求。
车架前部完成承载了悬挂、转向、电子系统、成员舱等。
空间管阵式车架的后部结构,承载了引擎、变速箱、悬挂等关键部件。
应该这样说,正是因为这种车架的随意性很大,所以开发者可以很有着重点地考虑车架的承载问题和安全等问题,既可以设计上的不断优化令整车刚性大幅提升,也可以将整体重量降到最低,所以即使整体体积巨大的超级跑车,比相同尺寸的房车等要轻上许多便是其优势所在,而且,更重要的是,它可以轻易承受那些讲求极致动力性能的引擎,所以其各种特殊便成了超级跑车们的最爱。
2、铝合金空间管阵结构
传统式的空间管阵式车架虽然在性能上无所挑剔,但是其管材是通过焊接完成的,而且管阵机构的随意性很大,对于大量生产根本就是天方夜谭。所以有不少的汽车厂家开始考虑如何将这种如此优秀的车架设计形式进行大量生产,其中,最早获得成功的是奥迪(AUDI)和本田(HONDA),两个车厂几乎同时推出了各自的铝合金空间管阵结构,前者将之应用在其顶级的大型房车A8和小型房车A2上,而后者则令NSX成为全球第一台铝合金车架的超级跑车。
现实中的AUDI A8车架。
厂房公布的三维图片,A8的空间管阵其实结合了一体化和管阵式各自的优点。
AUDI A2的铝合金管阵式车架结构同样简单,车架并
没有如一体化车架般,其车架就是整车的骨干所在。
NSX的设计同样精妙,对于有多年赛车经验的HONDA要设计这样的车架并无太大的困难。
目前,除了AUDI和HONDA外,已经有许多超级跑车或者其他量产车型采用这种铝合金空间管阵式车架,例如最知名的有法拉利的F360和F430等等,不过需要注意的是,铝合金虽然重量轻,硬度也得到有效的解决方法,但是其容易氧化和可燃等特性确实是许多车厂值得考量的。
文章至此,目前市场上能被见到的车架设计形式已粗略地进行了介绍。文章没有出现太多的专业数据和词汇,毕竟在中国汽车技术网上的读者多是车迷,而非汽车设计工作者,太多的专业或者会打消对这样复杂的事物的理解热情,毕竟笔者也只是一个车迷,并不是什么汽车设计从业人员,或者那些参数上的,设计优化上的理解让那些人去实现吧,我们只需要了解自己的车便足够了。
声明:本网站所收集的部分公开资料来源于互联网,转载的目的在于传递更多信息及用于网络分享,并不代表本站赞同其观点和对其真实性负责,也不构成任何其他建议。本站部分作品是由网友自主投稿和发布、编辑整理上传,对此类作品本站仅提供交流平台,不为其版权负责。如果您发现网站上所用视频、图片、文字如涉及作品版权问题,请第一时间告知,我们将根据您提供的证明材料确认版权并按国家标准支付稿酬或立即删除内容,以保证您的权益!联系电话:010-58612588 或 Email:editor@mmsonline.com.cn。
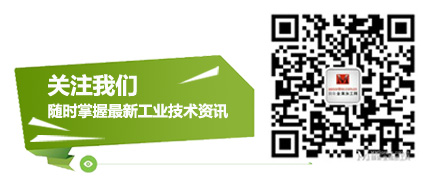
- 暂无反馈